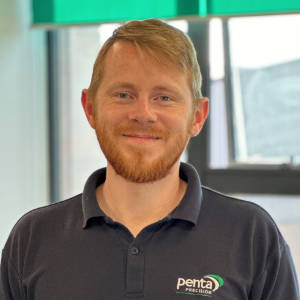
Cylindrical components bring their own unique challenges when it comes to manufacturing them. An experienced CNC machining company will be up for the challenge. But what about design? As a designer, your design can directly influence the function of your component, how efficiently it can be machined, and the machining time, and therefore costs.
In this blog, I’ll provide an insight into how cylindrical components are manufactured and give you my top 3 design considerations.
How are cylindrical components manufactured?
I’ll take this opportunity to shed a bit of light on how a CNC machining company like Penta might approach the manufacture of a cylindrical component. One might assume that all cylindrical components are turned on a lathe rather than milled on a milling machine.
However, it is possible to mill cylindrical components (although you can’t ‘turn’ non-cylindrical components), and there are often milling processes required on a turned component. For example, a cylindrical component may have other features that need to be machined that cannot be accessed by a lathe.
Additionally, there are ‘mill-turn’ machines. These are lathes that can also perform milling functions, meaning that some components can be manufactured entirely on a lathe. This approach is particularly beneficial for harder materials, where processes like stainless steel CNC machining require careful planning to maintain dimensional accuracy and minimise tool wear.
As a designer, you don’t need to worry too much about how your part will be manufactured. Your CNC machining company should be able to review your designs and choose the best solution. The ‘best’ solution is the one that is the most efficient and cost-effective for a particular design.
Designing cylindrical components
Where you will have more control as a designer of cylindrical components is in optimising your design to enhance component function, improve machining efficiency, and help keep costs in check.
For plastics in particular, design considerations can differ from metals due to material flexibility and thermal sensitivity, something worth bearing in mind if your project involves plastic machining.
Read on for my top 3 considerations when it comes to designing your cylindrical component:
1. Thickness of wall sections
Does your component need a thin wall? If a cylindrical component is designed with thin wall sections, there is a risk of the component being crushed or warped when held by the chuck, or when the component is released.
The chuck is what holds the workpiece in the machine and must grip tightly to ensure the component doesn’t move while being machined.
If the wall section is thin, the force needed to hold the workpiece in place can distort the component, making it hard to maintain the radius.
Similarly, when machining a component with a thin wall section, vibration may occur along the workpiece. This is an issue because it makes it difficult to hold tolerances and a consistent surface finish.
This isn’t to say that machining a cylindrical component with very thin walls isn’t possible! An experienced CNC turner will find a solution. However, it’s important to note that thin walls will require a longer set-up and machining time, which will in turn increase machining costs.
So the question to ask yourself is, does your component need very thin walls? If yes, you’ll need to factor this into your project timeline and costs. If not, choose a more reasonable thickness which will be quicker to machine and more budget-friendly.
2. Length of cylinder
Another design feature that can cause surface finish issues and difficulties in maintaining tolerance is related to the length of the component.
At the chuck end, the material will be held tightly and the rotation will be precise. However, the further away from the chuck, the greater the amplification of the rotation, which will cause a ‘wobble’.
A longer piece of material will also flex more during machining. Both of these factors will cause inaccuracies and the vibration will mean that the surface finish is compromised.
One solution to this is to use a centre, where a small recess is machined in the end of the component, so that it can be held steady at both ends.
For most applications this causes no issues, but it is worth considering when designing a component.
Machining without a centre is possible, but to achieve a suitable surface finish, a different solution would be sought, generally necessitating a longer set-up and machining time, which would, in turn, increase the cost.
3. Placement of features on either end
It can be challenging to ensure features match on each end of a cylindrical component. If they must match for the application, it is possible, but it will increase machining and set-up times and therefore cost.
If the features do not need to match exactly, you can specify this by writing ‘orientation not important’ on your design. This gives more freedom to the manufacturer to produce the component in the most efficient way possible.
Conclusion
When designing a cylindrical component, you don’t need to worry about how the part will be made. A trusted CNC machining supplier will handle that. What is within your control is ensuring that your part is designed with manufacturability in mind. This will help with efficiency and keeping costs in check.
Need some help with that? Partnering with a CNC machining company who also offer machining design advice can be invaluable. The right supplier will be able to advise you on your design to balance the varying priorities of form, function, efficiency, and cost.
Partner with Penta
Penta is an experienced machining company with strong expertise in both turning and milling. Our customers gain great value from our machining design advice.
We also have a mill turn machine which combines tool rotating and workpiece rotating functionality – the ultimate milling/turning hybrid. This can improve the speed, efficiency, and accuracy of machining more complex cylindrical parts.
If you would like to discuss how Penta can help you with your upcoming project, give our friendly and experienced estimating team a call on 023 9266 8334 or email .
You can also book a Discovery Call with us here.