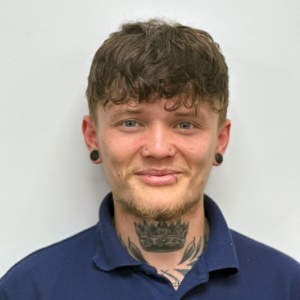
Surface finish may not be at the top of your list when it comes to designing your CNC machined component, however, it can play a vital role in the quality, aesthetics, functionality and overall cost of your final product.
In this blog, I’ll delve into the essentials of surface finishing and explore the five key factors every specifier and engineer should consider when deciding on the appropriate surface finish for their CNC machined part.
Surface finishing vs finishing processes: understanding the difference
For clarity, let’s make sure we’re on the same page. Surface finish is the machined finish before any additional finishing processes are applied. Often it is then appropriate for the component (or specified faces of a component) to undergo further processes, i.e. ‘finishing processes’ to further enhance performance or aesthetics. Common finishing processes include anodising, plating, and bead blasting.
Five factors to consider when deciding on your surface finish
1. Material considerations
The type of material chosen not only affects the ease and cost-effectiveness of machining but also dictates the achievable surface finish tolerance. Aluminium, for example, typically yields smooth results whereas stainless steel requires more time and advanced techniques and tooling to achieve a similar surface finish.
Additionally, the chosen material impacts the tools used during machining, which in turn, affects both the final surface finish and cost.
The specific material grade is another crucial factor as it can significantly impact the post-machining appearance, especially once finishing processes are applied.
For example, you could choose to make a component out of two varying grades of aluminium. After machining, the surface of either of these components may exhibit tool marks. The material grade becomes crucial when applying a finishing process such as anodising.
This is because variations in alloy composition can impact how different grades of aluminium respond to finishing processes. A grade such as 5083 is more likely to yield a more uniform and aesthetically pleasing finish after anodising than 7075.
To ensure a seamless process, it’s essential to create prototypes using your selected material and grade that incorporate specified surface finishes and any finishing processes. This will allow you to identify potential issues or areas for improvement.
2. Aesthetics
Aesthetics play a vital role in the visual appeal of the final product. As a designer, it’s important to decide where visible tool path lines are acceptable and where they aren’t. This is often the distinction between the customer-facing and internal faces of the component.
What we refer to as a ‘good machined finish’ for visible faces would be a surface finish of Ra1.6µm or better. For hidden or non-critical surfaces such as the interior of an electronics enclosure, the surface finish could be relaxed to Ra3.2µm or greater. Or to put this another way, here at Penta, we consider non-critical surfaces to be anything over 1.6 micrometres.
Additionally, you must factor in any planned finishing processes to achieve your desired aesthetic result.
3. Function
While surface finish is typically associated with aesthetics, it’s important to recognise that it does play a part in function. Here are some key examples…
Friction and wear resistance
A smoother surface finish reduces friction between moving parts, minimising wear and extending the lifespan of components. This is crucial for applications where components slide or rotate against each other.
Sealing and fluid flow
For components involved in sealing applications such as o-rings and gaskets, choosing an appropriate surface finish is essential. Excessive roughness can create gaps, allowing fluids or gases to leak, compromising seal integrity. A properly finished surface ensures tight, even contact between mating surfaces, promoting effective sealing, preventing leaks, and maintaining the integrity of the system.
Adhesion and bonding
The surface finish can affect bonding strength. For example, when applying adhesives or joining components through processes such as soldering or brazing, the surface finish will directly impact the strength and reliability of the bond. A rougher surface finish creates a larger surface area, promoting stronger adhesion and more durable bonds.
Electrical conductivity
In electronic components, the surface finish can affect electrical conductivity. A rougher surface can hinder the smooth flow of electrons and potentially increase resistance. A smooth and clean surface finish ensures reliable electrical connections, reducing the risk of signal interference and reducing heat generation.
4. Cost implications
Over-specifying surface finish can have a considerable impact on cost. As you may have guessed, a higher specification finish increases the machining time.
Additionally, it can accelerate the wear on cutters, particularly for harder materials such as stainless steel, and increase the likelihood of requiring specialist (and therefore more expensive) cutters.
A higher surface finish can also have an impact on packaging requirements. A lower specification surface finish can allow components to be stacked for shipping, whereas a higher specification may require individual wrapping.
Finally, consider the cost of surface finish on inspection requirements. More on that in the next section.
So, remember it is vital for you to strike a careful balance between cost and surface finish specification. Not all faces need to be equal so do consider relaxing the surface finish on non-critical or hidden faces. If in doubt, consult your CNC machining supplier.
5. Quality control/inspection requirements
Achieving high-tolerance surface finishes has implications for quality control and inspection processes. In-process and final inspections become more time-consuming and intricate, adding to the overall cost.
Above and beyond visual inspection, a high-specified surface finish may require additional 100% non-contact inspection, or additional inspection via the use of a microscope, coordinate measuring machine (CMM), shadow graph, surface testers or feeler books. Therefore, ensure your budget aligns with the required level of quality control.
The final step to surface finish success
As you can see, surface finish goes beyond surface level and is a key consideration in your CNC machined component. Rather than going it alone, it can be much more efficient and cost-effective to enlist the help of a Design for Manufacturability (DFM) service from an experienced CNC machining supplier.
This will be a process of analysing your design, taking into account the application and your budget, and making recommendations on design and surface finish, to keep your project on time and in budget.
Here at Penta, our DFM service has helped many designers like you. If you’d like a free consultation call about your next project, please get in touch with our estimating team, call us on 023 9266 8334 or email .
Who is Penta Precision?
Penta is a UK-based CNC machining company. We’re getting a reputation for not only the quality of our parts, but also our exemplary communication, the care we take with orders placed with us and the consistency of our service. You can find out more about us here.