Balancing Aesthetic and Functional Design in CNC Machined Components: A Guide
29th May 2024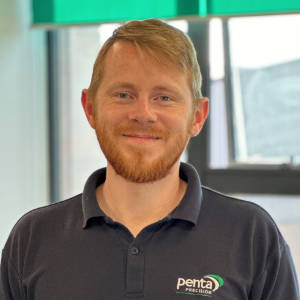
Imagine a component that turns heads with its sleek design but fails to perform its basic function. Or one that performs its purpose to perfection but gets overlooked for its clunky exterior.
Aesthetics vs functionality…the ongoing conflict in the minds of product designers and engineers. Striking just the right balance between these two crucial aspects (while keeping your project within budget) may be one of the most challenging parts of your role.
In this blog, I’ll look at aesthetic and functional design of CNC machined parts. I’ll take each in turn and cover the key factors. Then I’ll consider how you can balance the two and finally, outline some common trade-offs.
What is aesthetic design and when is it important?
I’m sure you’re well aware that aesthetic design refers to the overall visual appeal of a component. An additional aspect that is sometimes overlooked but equally important in some cases is the sensory appeal of the part. So, when considering aesthetic design, we’re looking at the look, feel, and overall design that makes a product attractive.
Consider the sleek lines and smooth finish of an iPhone. Or the intricate curves of the Lamborghini Murcielago Roadster’s alloy wheels. In these cases, visual appeal plays a significant role in user experience and brand perception.
As well as consumer electronics and automotive parts, luxury consumer goods also rely heavily on aesthetics to convey value and exclusivity.
Key factors in aesthetic design
There are several key factors involved in the aesthetic design of CNC machined components. I outline the most important below.
Material choice
The material chosen for a CNC-machined component can significantly impact the look and feel of a component. Each option offers unique visual and tactile qualities. But with so many options, how do you choose the right one?
When thinking about aesthetics, consider the visual characteristics. Brushed aluminium for example exudes a modern feel whereas brass can offer a warm, classic look. Engineering plastics can come in an array of colours, allowing for vibrant customisation.
Of course, it’s not just choosing a material but also narrowing it down further into a specific grade.
For example, there are a broad range of aluminiums that are suitable for machining. Of course the desired properties will be a factor, but we’ll get to that later. Aesthetically, there are variations too.
For example, 5083 has a bright, silvery appearance making it a popular choice for applications requiring a clean, modern look. Whereas 7075 boasts a slightly darker silver hue, giving it a more high-tech, premium aesthetic.
A good CNC machining company can help you distinguish between material grades.
Finishing processes
Finishing processes such as brushing, bead blasting, polishing, anodising, and powder coating can elevate the visual impact of your component. Back to the iPhone for example. Apple has invested millions into perfecting the perfectly smooth brushed aluminium casing that has become synonymous with quality.
Your component probably doesn’t require the same investment, but time and budget should certainly be allotted to getting the right finishing process.
Design features
Incorporating design features such as curves, patterns, and engravings have the potential to add to the aesthetic value of your product. They can add visual interest and perhaps more importantly, differentiate your product from others on the market. This can be imperative for brand positioning, particularly if yours is a product at the higher end of the market.
Colour and branding
Strategic use of colour and logos can reinforce your brand identity and make your product instantly recognisable. Though if you’ve excelled yourself on the design features I mentioned above, you may not need to brand your product. Some of the most recognisable products in the world have achieved notoriety from their distinctive design alone. A Coca-Cola bottle without a label would be clearly identifiable to most.
What is functional design and when is it important?
Functional design prioritises a component’s ability to perform its intended task flawlessly. It’s about ensuring the component is strong where it needs to be strong, durable where it needs to be durable, or perfectly toleranced to fit with mating parts.
Functional design is most important in safety-critical industries such as aerospace where components need to be exceptionally strong, lightweight, and able to withstand extreme temperatures and stresses.
Medical devices and surgical instruments are other components that often require precise tolerances and very specific materials.
Key factors in functional design
In this section I’ll explore the essential consideration for creating functionally robust CNC machined components.
Material properties
If you thought material selection was crucial for aesthetics, it becomes even more paramount for functionality!
Different materials and even material grades, have considerable variations to their properties.
Data sheets can be a good first port of call to help narrow your choice of materials or grades. Thereafter, you may wish to research multipoint data and even conduct testing yourself under the spectrum of conditions you expect for the finished product.
Some CNC machining suppliers can advise on material selection as part of a Design for Manufacture service.
Tolerance
Specifying a suitable tolerance for your CNC machined component is all about weighing up function with cost.
Achieving a very tight tolerance is time-intensive, for the machinist and quality inspector. It also requires specialist inspection equipment. Therefore, tight tolerancing can come with a premium price tag.
In certain instances where tight tolerances are imperative (safety-critical or closely mating parts), these costs must be factored in.
But for some components, a more open tolerance will be more appropriate. Our blog ‘Why tolerance matters’ is a good starting place for exploring appropriate tolerancing.
Structural integrity
Structural integrity is about ensuring your component can handle operational stresses and have a long lifespan.
The first aspect to consider is design geometry. I recommend avoiding sharp corners which can concentrate stress, leading to cracks, and instead using fillets or rounded edges.
You should ensure uniform wall thickness to prevent weak spots. You may also choose to strategically add thickness to certain faces where strength matters most.
Additionally, you can consider incorporating features such as ribs (thin walls extending from the main body) or gussets (triangular shapes connecting walls) to reinforce areas under high stress without adding bulk.
Ease of manufacturing
When designing a component to be CNC machined, there is always a balancing act between the functionality of the part and associated costs. A more complex part will have increased machining time and therefore a higher cost. Your finished product needs to be economically viable and therefore all components need to be carefully costed.
Balancing aesthetic and functional design
As in many areas of life, the key to success is finding balance. In this case, pursuing the perfect compromise between visual appeal and functionality.
It’s worth taking the time early in your design process to consider where your priorities lie. If your end product is more high-end with a price point to match, you won’t need to make as many concessions in the component design because you’ll be able to pay for both aesthetics and functionality.
But for most of us, compromises will need to be made in one area or the other.
I recommend a collaborative design process, bringing a CNC machining partner on board early. It can be disheartening to finish a design, only to discover that it would be complicated and expensive to machine, or worse still, unmachinable (unfortunately this does happen occasionally – we get sent geometrically impossible designs!).
Choose a CNC machining provider who specialises in Design for Manufacturability (DFM) to help you achieve the appropriate balance between aesthetics, form, fit, function, machinability, and cost.
Be sure to prototype and test your design thoroughly before committing to full production. This will allow for early identification and correction of any functional or aesthetic shortcomings and help you achieve the most suitable balance between the two.
Common trade-offs
If you’re still wondering how concessions to aesthetics or functionality can be made in order to keep your project within budget, I thought I’d outline here a few trade-offs that we often guide our customers to make.
Surface finishes
Over-specifying surface finish is a sure-fire way of inflating costs. Yes, some faces may require a ‘good machined finish’ of Ra1.6µm or better, but what about hidden faces?
A common example is the interior of an electronic enclosure. This is non-customer facing, non-critical, and could have a more relaxed surface finish of Ra3.2µm or greater. A lower specification finish will expedite machining on those surfaces so that more time can be taken on surfaces that are more aesthetically important.
Similarly, a selected finishing process doesn’t need to be applied to every surface. Could you save money on hidden faces in your design so that you can invest more in customer-facing surfaces?
Material selection
Material grades are another area where compromise can and likely will, need to be made. When choosing a material, it’s not just the aesthetic appeal or functional properties that must be considered. A further two major considerations are weight and machinability.
In aerospace components, for example, aluminium is commonly used as it is lightweight and has good machinability – but for certain applications titanium may be preferred due to its superior strength and even greater weight savings. Titanium will however come at a much higher cost and is more challenging to machine. It’s important to consider whether the trade-off for strength and weight saving is so critical to the function of the final component.
Material grade vs finishing process
Another common and often overlooked consideration when balancing function and aethetics is the trade off between a material or material grade and the requirement of a finishing process.
Often a product designer may select a higher specification grade of material due to it's aethestic benefits. However, if the component is then going to be anodised, the benefits of the higher grade of material may become irrelevant. As an example, if choosing an aluminium alloy, a designer may select the more expensive 7075 grade, when a cheaper and more readily available 6082 grade could offer a very similar final component if it is put through a sulphuric anodising process.
It is also important to note that a good surface finish or finishing process may be needed for a product to meet functional requirements. For example, certain components exposed to chemicals or fluids may require a surface finish, such as Hard Anodising to help protect it against corrosion or reduce friction (with mating parts).
For more information, find our comparison of Hard Anodising Vs Sulphuric Anodising blog here.
It is important to speak to a trusted CNC machining partner to understand the intricacies of anodising and the impact that will have on your final component. This includes and how the material grade selection will impact the final component's fit, form and function.
Curves and rounded edges
A common design consideration is the use of curved or rounded edges. Functionally, curves and rounded edges can help distribute stress and improve the durability of a component. It can also be crucial for components subject to flow (of fluids or gases) as it can reduce turbulence and improve flow characteristics.
Aesthetically, curved and rounded edges can also make a component more visually appealing and ergonomic, being safer to handle with less sharp edges.
The key trade off here is often the cost and machining time. Many curved or rounded edges will be more complex and expensive to machine – it’s important to consider whether the curves are purely aesthetic or offer a functional benefit too. It may also be good to consider chamfered/bevelled edges rather than curved as they can be slightly less complex to machine but offer some functional benefits.
A winning combination
Balancing aesthetic and functional design in CNC machined components is essential for creating successful products. By considering your priorities, the key factors of each and looking at where trade-offs can be made, you can find the right balance between the two and still keep your project within budget.
Need some help?
This is a complex balancing act and sometimes it’s best to consult the experts. Here at Penta, we offer a highly rated design for manufacture service which includes finding the right balance between aesthetic and functional design, alongside the practicalities of machining a part and keeping your project within budget.
If you’d like a no-obligation conversation about your project, please get in touch with my team on 023 9266 8334 or email .