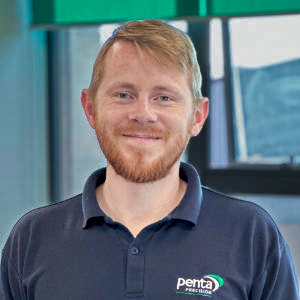
Environmental responsibility is becoming a key consideration in modern manufacturing. Green machining offers a smarter, more sustainable way to produce high-precision components without compromising on quality or performance. As industries adapt to changing expectations, sustainable machining is becoming essential for staying competitive and future-ready.
This blog explores how CNC machining can be made more sustainable across every stage of production. You'll learn about the environmental impact of CNC processes, discover practical green manufacturing strategies, and explore both the benefits and challenges of going greener. Whether you're an engineer, buyer, or manufacturer, these insights will help you make more informed and future-ready sourcing decisions.
Environmental Impact of CNC Machining
Understanding the environmental impact of CNC machining is the first step towards making your operations more sustainable. Although CNC processes are known for their precision and efficiency, they still rely heavily on electricity and raw materials. Every aspect, from energy usage to waste disposal, affects your overall environmental footprint.
Energy Use
CNC machines run for long periods and often require high-speed operation, leading to heavy electricity consumption. Motors, drive systems, cooling units and control interfaces all contribute to total energy draw. Without energy-efficient upgrades, the environmental impact of CNC machining can quickly escalate across large-scale facilities.
Cutting Fluids and Lubricants
Cutting fluids are essential for temperature control and surface finish but often contain synthetic chemicals that are difficult to dispose of safely. If these fluids are not managed properly, they can leak into local water supplies or harm the surrounding ecosystem. Sustainable machining requires choosing safer alternatives and ensuring responsible fluid handling practices.
Emissions and Pollution
CNC machining may release fine particles, mists, and volatile organic compounds (VOCs) into the air. These emissions can affect both indoor air quality and external environmental conditions if not filtered or controlled. The energy required to power machines also contributes to CO₂ output, further amplifying the impact CNC machines have on the environment.
Material Waste
CNC machining is a subtractive process, meaning excess material is cut away to shape the final part. This generates significant scrap in the form of swarf, offcuts, and unused stock. Even when working with high-precision techniques, material waste still builds up unless processes are closely optimised.
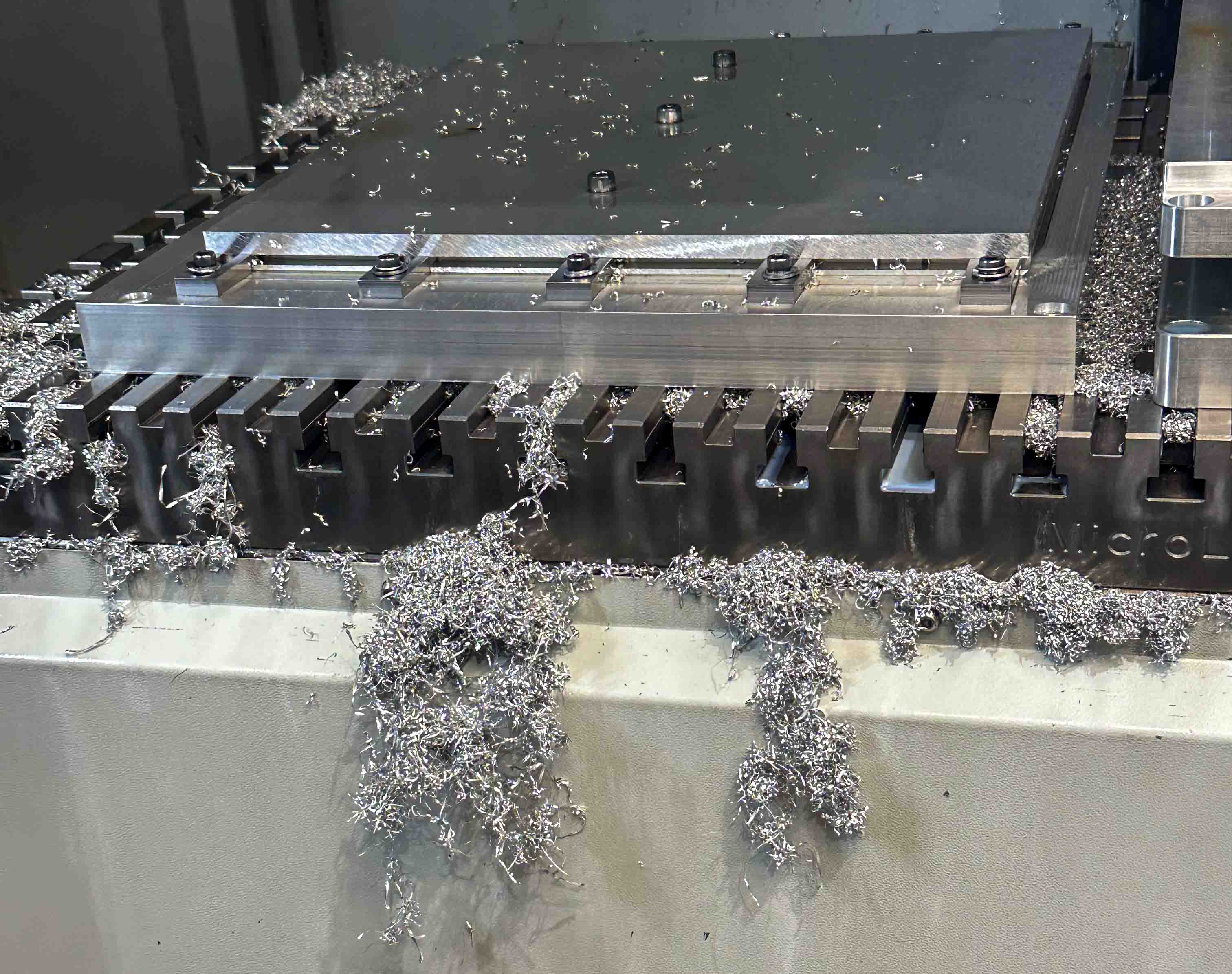
Sustainable CNC Machining Practices
To reduce negative effects, many manufacturers are adopting green machining strategies tailored to the CNC environment. These include energy-saving equipment, smarter waste management, and eco-conscious material choices that reduce the environmental impact of CNC machining. When assessing potential suppliers, look for those who prioritise sustainable machining innovations and continuous improvement.
Energy-Efficient Machines
Modern CNC machines are often equipped with inverter-controlled motors and built-in energy management systems. These technologies help lower energy consumption by adjusting speeds and reducing idle power draw. Facilities may also implement smart lighting systems and track usage through monitoring software for ongoing efficiency gains.
Reducing Material Waste
Reducing waste starts with better planning and smart production methods. Nesting software, advanced CAD/CAM integration, and real-time stock tracking all help minimise excess and reduce scrap. Suppliers who adopt just-in-time manufacturing can significantly lower both raw material use and warehouse waste.
Eco-Friendly Cutting Fluids
Eco-friendly cutting fluids are typically made from plant-based oils or biodegradable compounds. These fluids are designed to perform well while reducing environmental harm and improving workplace safety. Using them as part of your green machining approach can support both sustainable manufacturing and regulatory compliance.
Recycling and Reuse
Green manufacturing involves reclaiming scrap materials like swarf and offcuts for reuse or recycling. Many CNC shops now repurpose leftover stock or sell it back into the supply chain to reduce waste. This sustainable approach often extends to value-added processes, including surface finishing solutions that reduce the need for rework and material loss.
Dry and Near-Dry Machining
Dry machining eliminates the need for cutting fluids, making it one of the cleanest machining methods available. Near-dry machining, or minimum quantity lubrication (MQL), applies a controlled mist of lubricant to the cutting zone. These practices support sustainable machining by improving air quality and reducing disposal requirements.
Benefits of Green Machining
Investing in green machining has clear advantages for both manufacturers and their customers. It helps reduce the environmental impact of CNC machining while supporting stronger business performance. For procurement teams, working with sustainable partners can also boost brand reputation and support ESG and compliance goals.
Some of the key benefits include:
- Lower operational costs from reduced energy and cutting fluid usage
- Faster compliance with environmental regulations and reporting standards
- Improved customer appeal among sustainability-focused buyers
You also benefit from suppliers who are focused on innovation and long-term efficiency. Those adopting green manufacturing often have better processes, shorter lead times, and stronger quality control systems. This leads to more consistent results without compromising your deadlines or technical requirements.
Challenges in Sustainable CNC Machining
Despite its benefits, green manufacturing comes with several hurdles for businesses to navigate. Upgrading equipment, improving infrastructure, or integrating new systems often involves high upfront costs. For smaller operations or legacy facilities, this investment can delay the shift to sustainable machining.
It also takes time and training to implement new techniques like dry machining or energy monitoring. Adopting these methods often requires a change in workplace culture, not just equipment. Balancing production output with sustainability goals can be difficult during periods of high demand.
Another challenge is the lack of consistent sustainability standards across the machining industry. Without common benchmarks, comparing supplier credentials can be unclear or misleading. That's why it's essential to ask specific questions and look for relevant certifications when assessing green machining capabilities.
Final Thoughts Sustainable CNC Manufacturing
Green machining is no longer a niche concern, it's a strategic advantage in today's manufacturing landscape. By reducing emissions, energy consumption, and material waste, it helps future-proof your supply chain. Choosing a precision CNC machining partner that prioritises sustainability is a smart move for your business and the planet.
Companies like Penta Precision are leading the way with ISO 9001:2015 certification, efficient supply chain management, and deep expertise in complex materials. We provide complete support from collaborative design through to dependable delivery. Our focus on high-performance components ensures every project is executed with care, consistency, and environmental responsibility.