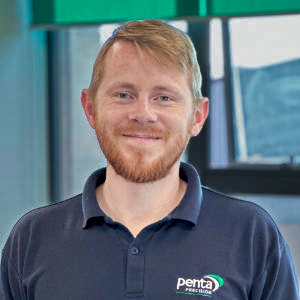
Material selection plays a critical role in the success of any machining project. Choosing between hard and soft metal machining can significantly impact your production time, overall cost, and the quality of your final part. Each approach has its own strengths, limitations, and ideal use cases.
In this guide, we'll explore the key differences between hard and soft machining, including materials, tooling, finishes, and industry applications. You'll also learn how to choose the best approach based on your part design, production volume, and budget. Whether you're working on a prototype or a full-scale production run, this blog will help guide your decision-making process.
What Are Hard Metals?
Hard metals are materials that resist deformation, abrasion, and wear under extreme mechanical stress. In CNC machining, the term often refers to metals that have been heat-treated or hardened through processes like quenching or case hardening — typically achieving a hardness of 45 HRC or higher. This includes both inherently hard materials and those that have been made harder through heat treatment to improve strength, durability, and machining performance.
Common Types
Common examples of hard metals include titanium, tungsten, and hardened tool steels. These materials may be naturally hard or further strengthened through heat treatment to meet demanding application requirements. Due to their strength, they require robust, wear-resistant tooling for effective machining.
Key Applications
Hard metals are frequently used in aerospace, defence, and automotive industries where structural reliability is critical. Applications include fasteners, medical instruments, and components exposed to friction or heat. These parts must consistently perform under stress without risk of failure.
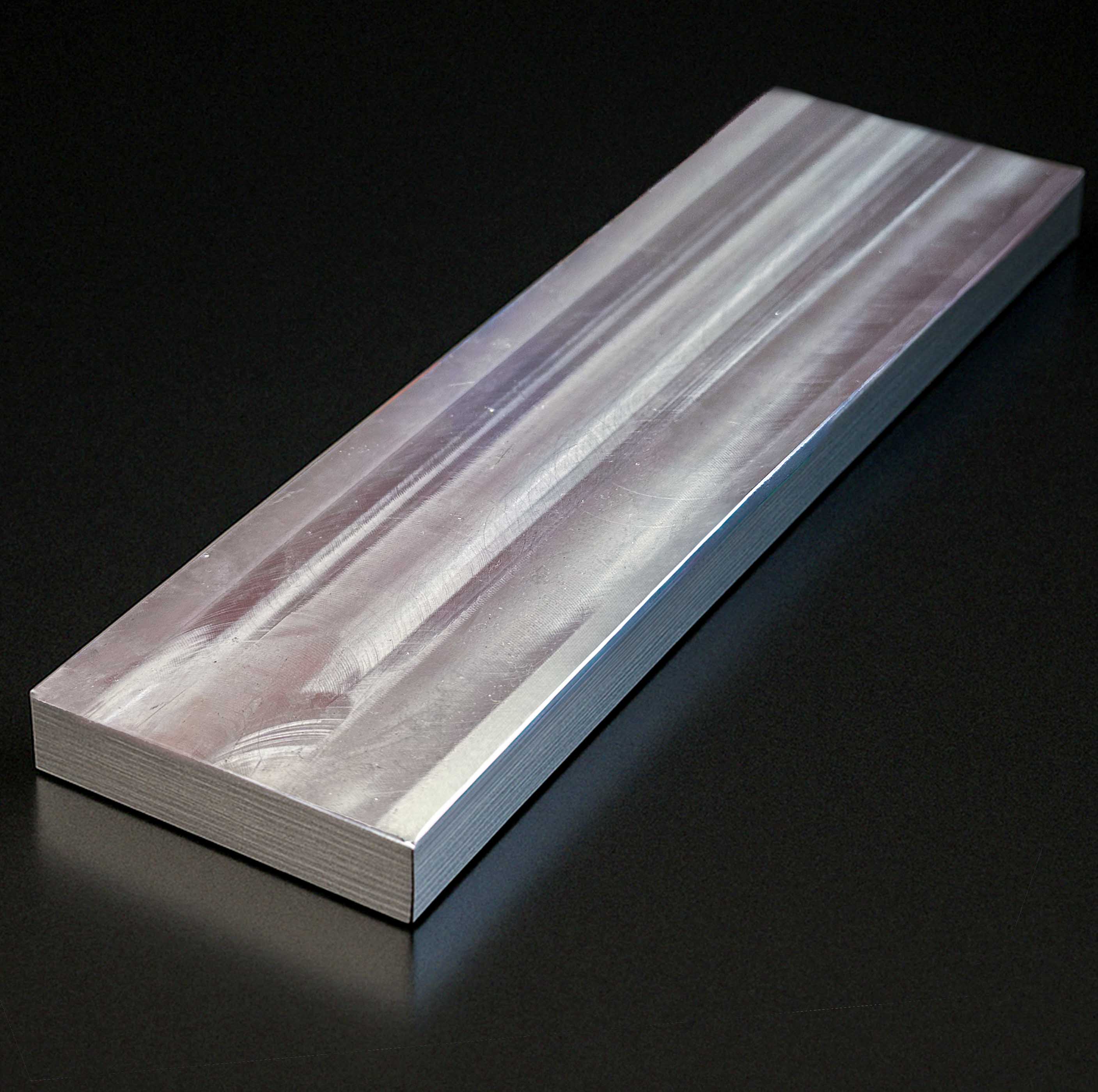
What Are Soft Metals?
Soft metals are more ductile and easier to cut, bend, and shape during machining. They require less force to machine and produce significantly less heat than harder materials. This makes them ideal for low-stress components, aesthetic parts, or applications where ease of shaping is a priority.
Common Types
Common soft metals include aluminium, brass, copper, zinc, and lead. These materials are favoured for their lightweight properties and are frequently used in prototyping and electronics. Their excellent thermal and electrical conductivity also makes them ideal for use in electrical systems and connector components.
Key Applications
Soft metals are commonly found in consumer goods, electronic housings, medical devices, and lightweight aerospace parts. Components such as aluminium enclosures and copper terminals are well suited to soft machining. These parts benefit from smooth surface finishes and high dimensional accuracy, especially when tight tolerances are required.
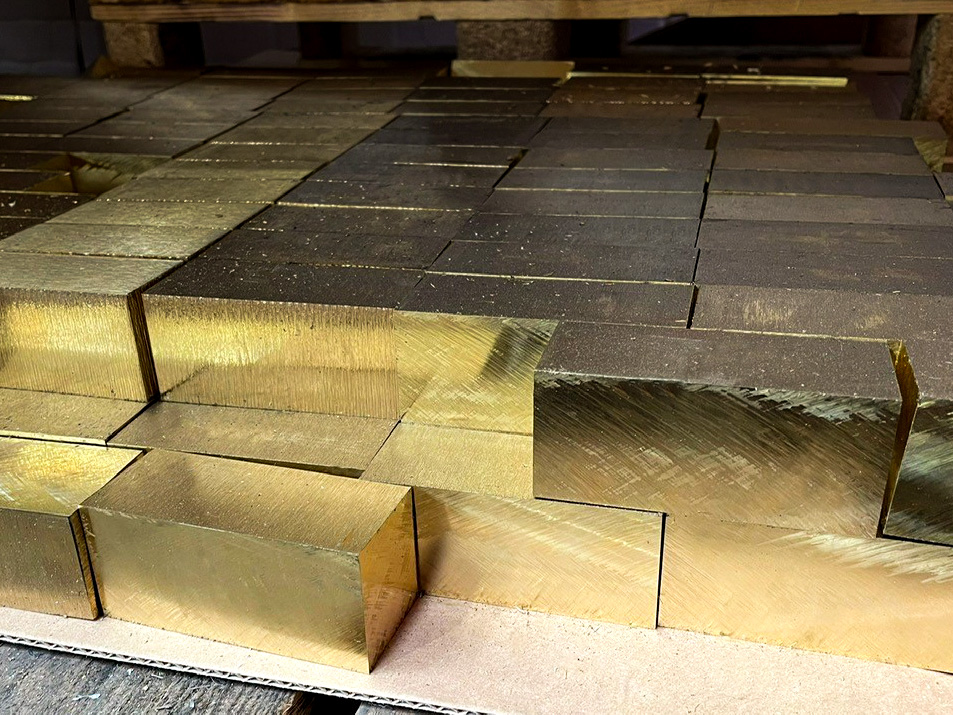
Machining Techniques for Hard and Soft Metals
Machining techniques must be adapted to suit the material being used, particularly when comparing hard and soft metals. Tool choice, feed rates, and cooling strategies all vary depending on the hardness and properties of the material. Understanding these key differences helps improve part quality, tool life, and overall machining efficiency.
Tooling Needs
Hard machining relies on carbide or coated tools designed to withstand high temperatures, abrasion, and cutting pressure. These tools are essential when machining hardened metals, which are more abrasive and difficult to cut than untreated ones. For soft machining, machinists often use standard HSS tools or soft tooling, which is more affordable and easier to swap out when needed.
Cutting Speeds & Feeds
When machining hard metals, slower cutting speeds and reduced feed rates are essential to prevent excessive heat and tool damage. These materials resist cutting, so aggressive machining can compromise surface finish and dimensional accuracy. Soft machining allows for faster speeds and higher feeds, enabling quicker cycle times without sacrificing part quality.
Cooling & Lubrication
Hard metal machining generates a large amount of heat, making efficient cooling and lubrication essential to protect both the tool and the workpiece. Without proper cooling, tools can fail prematurely, and thermal distortion can affect tolerances. In soft machining, cooling is still important, particularly with plastics, but must be carefully managed to prevent warping, melting, or material degradation.
Comparing Hard and Soft Metal Machining
Understanding the trade-offs between hard and soft metal machining is key to selecting the right method for your project. Each approach performs differently when it comes to speed, tooling, finish, and cost. The following breakdown will help you compare performance across essential machining metrics.
Category | Soft Metals | Hard Metals |
---|---|---|
Machinability & Tool Wear | Easier to cut; low tool wear | Higher wear; tools replaced often |
Cutting Speeds & Feed Rates | Higher speeds; ideal for fast runs | Slower speeds to protect tools |
Surface Finish & Tolerances | Good finish; may deform without care | Excellent finish; tight tolerances |
Heat Generation & Cooling | Lower heat; minimal cooling needed | High heat; cooling essential |
Tool Life & Maintenance | Longer tool life; less maintenance | More wear; higher maintenance |
Costs & Efficiency | Cheaper for low-volume/prototyping | More expensive; suited to high-performance parts |
Machinability & Tool Wear
Soft metals are easier to cut and shape, resulting in low tool wear and longer tool life. Tools can be reused across multiple jobs with minimal maintenance or adjustment. Hard metals, on the other hand, wear tools quickly, increasing the need for replacements and recalibration.
Cutting Speeds & Feed Rates
Soft machining enables higher cutting speeds and feed rates, which makes it ideal for fast production runs. It suits rapid prototyping, low-volume batches, and quick turnarounds. Hard machining demands slower speeds to maintain precision, reduce tool strain, and avoid overheating.
Surface Finish & Tolerances
Hard machining delivers excellent surface finishes and ultra-tight tolerances, which are critical in aerospace, surgical, and automotive parts. Soft machining also achieves good finishes, especially on materials like aluminium and plastics, though it can be prone to burrs or deformation. Careful tool selection and accurate cutting parameters can help maintain part quality.
Heat Generation & Cooling
Hard metals create more friction and heat during machining, so effective cooling and lubrication systems are essential. Without them, tools may overheat and parts can suffer from warping or dimensional shifts. Soft materials generate less heat overall but still require some cooling, particularly with thermoplastics.
Tool Life & Maintenance
Soft tooling generally lasts longer when used on ductile, low-resistance materials. Reduced friction and stress lead to less frequent tool replacements and lower maintenance costs. In contrast, hard metal machining wears down tooling more quickly, increasing downtime and operational expense.
Costs & Efficiency
Soft machining is cost-effective for low-volume or prototype machining, thanks to cheaper materials and faster processing times. Setup is simpler, and tooling costs are generally lower. Hard metal machining is more expensive due to advanced tooling needs and slower cutting speeds, but it's essential for high-performance, load-bearing components.
Soft machining is best for:
- Rapid prototyping
- Lightweight components
- Low-volume production
- Soft or ductile materials
Hard machining is best for:
- High-tolerance parts
- Structural or load-bearing components
- Aerospace or defence industries
- Wear-resistant materials
Industry Applications
Soft machining is popular in sectors like electronics, consumer goods, and medical manufacturing, where detail and accuracy are important. It's ideal for producing housings, connectors, and plastic medical parts from materials that don't require high cutting force.
Hard metal machining is commonly used in aerospace and defence applications, where durability is key. While not all components require full hard machining, many projects involve materials like stainless steel or tool steel that are selected for their ability to withstand heat treatment and stress. Explore our stainless steel machining capabilities to learn more.
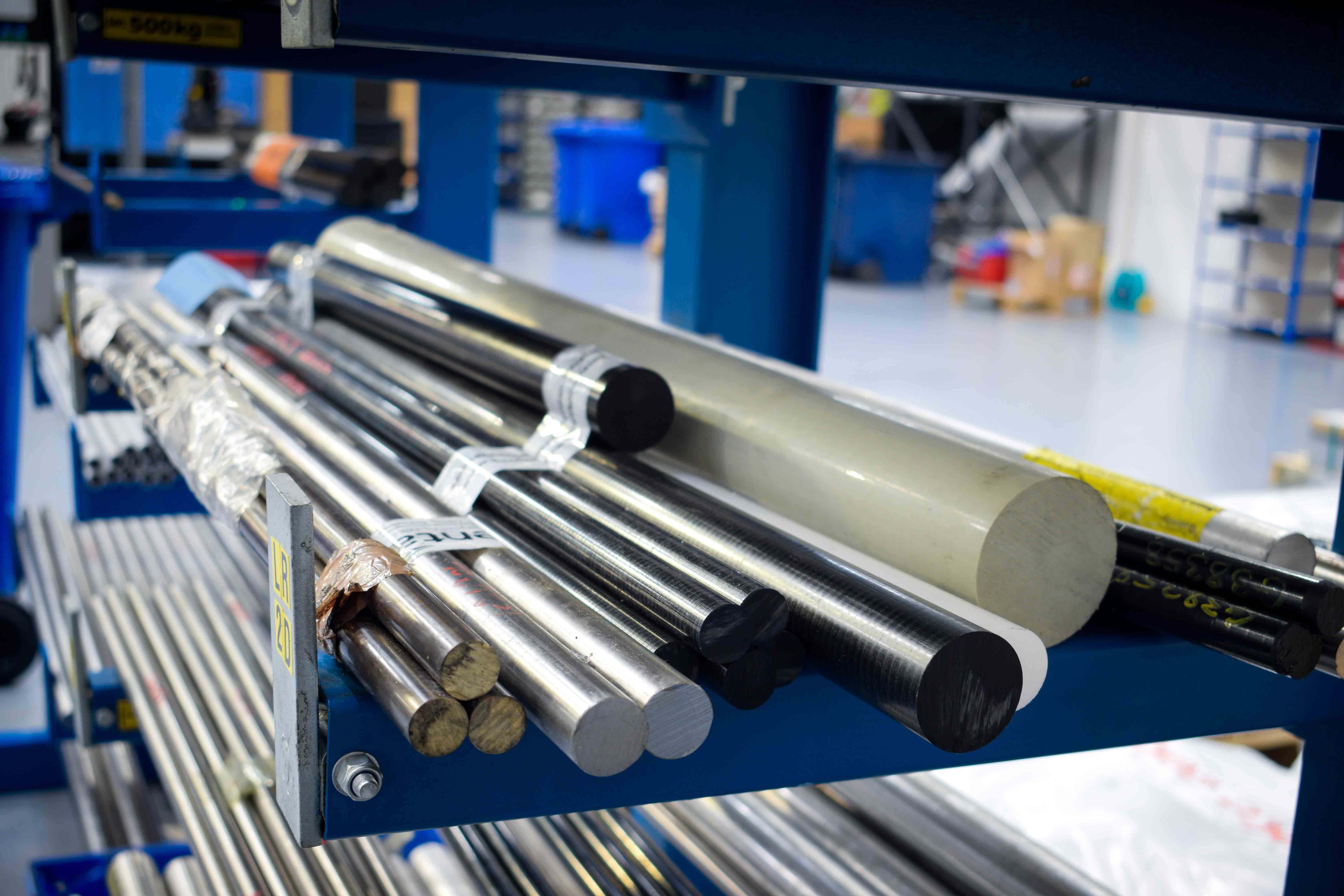
Choosing Between Hard and Soft Metal Machining
Your project's requirements will ultimately determine whether hard or soft machining is the right choice. Factors such as part geometry, production scale, and cost targets should guide your decision-making process. Below are key points to help you evaluate which approach suits your needs.
Design Needs
Soft machining is well suited for parts with intricate features, thin walls, or delicate materials that can't withstand high cutting forces. It allows greater flexibility in creating complex geometries without compromising the structure. Hard machining is better for rigid, load-bearing parts that demand strength, accuracy, and tight tolerances.
Production Volume
Soft machining is a cost-effective solution for prototypes and small batches, especially when quick iterations are needed. Its lower setup and tooling costs make it ideal for short-run projects. Hard machining becomes more economical for high-volume production, where investment in tooling and fixtures can be spread across larger quantities.
Material Cost & Availability
Soft metals and engineering plastics are generally less expensive and easier to source than hard metals. This makes soft machining appealing for budget-conscious projects or when quick material turnaround is needed. Hard metals tend to cost more and may involve longer lead times, particularly for niche or high-performance alloys.
Key Takeaways for Choosing the Right Machining Approach
Matching your material to the appropriate machining technique is key to achieving reliable, cost-effective results. Hard machining is the right choice when strength, tight tolerances, and performance under pressure are non-negotiable. Soft machining provides a more flexible and economical option for parts with simpler requirements, where finish and speed are the priority. Not every project requires fully hardened metals — in many cases, machinable materials with moderate hardness or post-processing potential offer the right balance of strength, precision, and efficiency.
FAQs