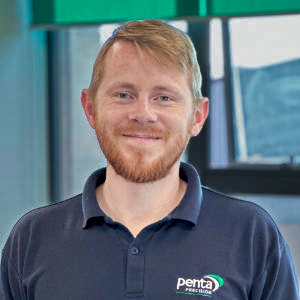
Just-in-time manufacturing (JIT) has reshaped how you manage production and inventory in today's fast-moving industries. By focusing only on producing what is needed, when it's needed, you avoid overproduction and save valuable resources. This lean, agile approach helps improve efficiency across your entire operation.
It's especially useful when working with high-precision, custom machined parts. With less waste and better timing, you reduce overheads and keep your supply chain flowing smoothly. Partnering with a reliable manufacturer like Penta Precision ensures your components are delivered on time and to spec.
What is JIT Production?
JIT production is a manufacturing strategy that aligns raw material orders and production schedules with real-time customer demand. You receive goods just in time for their use, rather than storing large quantities on-site. This helps reduce overheads, improve cash flow, and keep your operations lean and focused.
This approach is known as a "pull" system, where production only begins once an order is placed. Instead of forecasting large volumes, you focus only on what’s needed. Key benefits of this model include:
- Lower inventory holding costs
- Reduced waste and overproduction
- Faster, more efficient workflows
The concept of just-in-time manufacturing originated in Japan and became well-known through the automotive industry. Since then, it has been widely adopted in sectors like electronics, food service, and on-demand production. No matter the industry, the goal is the same: deliver exactly what is needed, exactly when it's needed.
Key Components of JIT Production
To implement JIT production successfully, several core elements must work in harmony. Each one plays a role in improving responsiveness, consistency, and overall output quality. Together, they form the backbone of a lean, efficient, and reliable JIT production system.
Total Quality Management (TQM)
TQM ensures that every part of your production process is focused on high-quality outcomes. You aim to produce right the first time, which reduces rework and eliminates unnecessary waste. This is essential for keeping your JIT production process smooth and efficient.
You involve your full team in maintaining these standards. Everyone takes ownership of quality, from machine operators to management. This shared mindset supports the long-term success of your JIT management approach.
Kanban System
The Kanban system is a visual scheduling method that helps you manage workflow in real time. It signals when materials are needed, ensuring you never order too much or too little. This keeps your operations running without excess stock.
Using Kanban, you can easily track where each product is in the production cycle. It helps you spot delays or inefficiencies before they become problems. As part of a broader JIT production system, Kanban plays a critical role in staying lean and responsive.
Supplier Relationships
Reliable supplier partnerships are key to keeping your just-in-time JIT production model functioning. You depend on accurate, on-time deliveries to avoid costly downtime and delays. Even one missed shipment can bring production to a halt.
Forming close, long-term supplier relationships gives you more control and flexibility. Working with local or highly responsive vendors can help speed up delivery times. A dependable supply chain builds resilience into your JIT production process.
Continuous Improvement (Kaizen)
Kaizen refers to the ongoing effort to improve your processes, one small step at a time. Your team constantly looks for ways to reduce waste, enhance workflow, and improve output. This approach keeps your production agile and competitive.
In JIT production, continuous improvement is more than a philosophy, it's a necessity. Every improvement, no matter how small, can strengthen your operation. Over time, these changes create a more reliable and efficient production environment.
Lean Manufacturing Principles
Lean manufacturing complements just-in-time manufacturing by focusing on eliminating non-value-added activities. You streamline operations to avoid delays, reduce excess inventory, and simplify workflows. This ensures that every action supports your bottom line.
While JIT production increases efficiency, lean manufacturing ensures the customer is always front and centre. The combination leads to faster delivery and higher quality products. Together, they help you stay competitive in demanding industries.
Inventory Management Strategies
JIT inventory strategies focus on reducing the stock you hold at any one time. You rely on precise forecasting and close coordination with suppliers to replenish only what's needed. This reduces overhead and keeps cash flow healthy.
Because your buffer is minimal, your system must be accurate and responsive. A single forecasting error could disrupt your workflow or delay delivery. Strong inventory control is essential to a successful JIT production system.
Production Scheduling Techniques
Effective scheduling aligns production with actual demand, rather than predictions. You allocate resources based on real-time needs, helping to prevent overproduction or wasted capacity. This creates a more stable and predictable operation.
Modern scheduling tools can help you optimise each production run. You can adjust quickly to changing requirements or supply chain issues. These techniques are critical to keeping your JIT production process on track and efficient.
How JIT Production Works
JIT production works by aligning your supply chain and manufacturing process with real-time customer demand. You only order materials when they're needed for a specific job, which avoids holding excess inventory. This shift helps you streamline operations and make more efficient use of your resources.
Imagine building a product only after a customer places their order. Each component arrives just in time to be used on the production line, never too early and never too late. This helps you:
- Avoid storage delays and costs
- Improve throughput across the production cycle
- Keep workflows lean and tightly controlled
This approach is especially effective in fast-moving sectors like automotive, electronics, and tech manufacturing. You can reduce lead times, minimise waste, and adapt quickly to customer-specific requirements. JIT management supports a more agile, responsive, and customer-centric way of working.
Advantages of JIT Production
The advantages of JIT production span both financial and operational areas. By holding less inventory, you cut storage, labour, and material costs significantly. This also frees up working capital to invest in other parts of your business.
With JIT, you focus on quality right from the start of production. Fewer errors mean less rework, fewer delays, and a more efficient use of time. It also results in a cleaner, more organised workspace, which supports better performance, benefits include:
- Faster production cycles
- Lower overhead costs
- Improved cash flow
- Less waste and fewer defects
- Greater responsiveness to customer orders
Disadvantages of JIT Production
Even with its benefits, there are some disadvantages of JIT production that must be carefully managed. You depend heavily on your suppliers, and even small delays can bring your operation to a stop. If forecasting is inaccurate, you risk missing deadlines or losing orders altogether.
Because there is little to no buffer stock, your business becomes more vulnerable to disruptions. Events like natural disasters, transport issues or supplier problems can quickly impact your workflow. JIT management demands a highly reliable and agile supply chain, challenges include:
- No room for error or delays
- Greater pressure on operations
- Vulnerability to external disruptions
- Limited flexibility for sudden large orders
Implementing JIT Production
Switching to a just in time JIT production system takes careful planning and the right support. You'll need to invest in staff training, update your internal processes, and build strong supplier partnerships. Collaboration between departments like purchasing, operations, and logistics is essential to make it work.
Start by reviewing how accurate your forecasting tools are and whether they can handle fluctuating demand. Your workforce and supply chain must be flexible enough to adapt to last-minute changes. If implemented correctly, you'll experience measurable improvements in cost efficiency and overall quality.
If you're in the early stages of adopting JIT, working with a machining partner that offers flexible support can make a real difference. Services like prototype machining solutions allow you to test, iterate, and refine your product designs before committing to full production. This minimises risks and helps you build confidence in your JIT process from day one.
Final Thoughts on JIT Production
JIT production gives you a competitive advantage when it's implemented with attention to detail and strong planning. With the right tools, supplier relationships, and cross-functional collaboration, you can streamline operations and reduce waste. It's an ideal approach for businesses that value speed, precision, and adaptability.
To support your goals, Penta Precision offers CNC machining services for both low and high-volume manufacturing. Our team understands the fast-paced needs of modern production and delivers consistent, high-quality results. With the right partner, your journey into just-in-time manufacturing becomes smoother, more efficient, and more scalable.