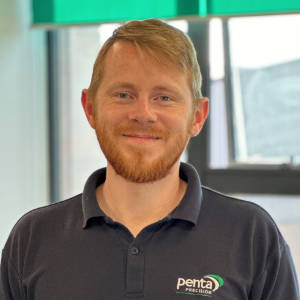
Imagine deploying your latest underwater sensor system, only for it to fail due to a faulty seal. This is a likely scenario when design and manufacturing aren’t aligned for underwater applications.
You don’t need me to tell you that when designing products for subsea or marine technology applications the stakes are incredibly high. The unforgiving marine environment demands components that are perfectly corrosion-resistant and watertight. Attention to detail is crucial here.
In this blog, I’ll guide you through the key decisions necessary to ensure your subsea components are up to the challenge. From selecting the right materials to choosing a CNC machining supplier that can meet the rigorous demands of marine applications, these tips will help you navigate the complexities of designing for the deep blue.
Dive in to discover how to avoid common pitfalls and ensure your components excel in the harshest of environments.
Which material should you use for your underwater housing or marine application?
Depending on the specific underwater application and function of the end product, there are several options available to you. For example, marine autonomous systems will have different needs to underwater sensing technology or surveying technology, and systems operating in saltwater will need different corrosion resistance to those operating in fresh water. These are just some of the many considerations that face a designer of underwater technology systems.
Let’s run through a few of the most likely candidates…
Naval brass – the obvious choice for marine technology applications
Naval brass (C46400) is the classic material used in marine environments. It’s strong, hard and corrosion resistant. An alloy of copper, zinc and tin, naval brass is very easy to machine.
However, it’s heavy, and that may not be appropriate for some technical or electronic systems designed for subsea environments. It’s more commonly used for marine hardware such as propellers, shafts and decorative fittings.
What about aluminium for marine technology?
The 5000 series of aluminium is a lighter alternative to brass. Consider aluminium 5083 for marine applications – it’s a medium strength manganese-chromium-aluminium alloy that’s highly resistant to seawater and can be anodised to provide further protection.
Plastics have a place in subsea technology too
Other lightweight alternatives to brass include a range of plastics. Acetal (POM) is commonly used, thanks to having good corrosion resistance, low water absorption, high strength and rigidity, and good compressive strength.
This is particularly important when operating in harsh environments: if your system gets knocked or dropped, an acetal housing will keep any electronics inside safe from damage.
Note: there are two types of acetal – copolymer and homopolymer. Delrin is a brand name for a specific acetal homopolymer. You can read more about the difference between Acetal and Delrin in our recent blog.
For more information about materials commonly specified for underwater environments, take a look at our materials resources.
How to ensure an underwater housing will be watertight
If you’re designing a system that will be housed in some kind of enclosure, any underwater housing must of course be watertight. It’s not just the material choice that’s relevant – getting the design right is imperative.
There are several ways that a watertight enclosure can be designed, and they all rely on the machining company achieving tight tolerances and a good machined finish. Sometimes it’s cleverly designed mating parts, perfectly executed.
Alternatively, a design may make use of a series of channels or recesses that will house O-rings, or use nitrile or neoprene gaskets to achieve the failsafe seal.
In theory, these methods are straightforward. And they are, at design stage! It’s when it comes to realising the design through manufacture that the theory can become problematic.
Usually, injection moulded components will not have the level of repeatable quality that is required to ensure a faultless seal for underwater applications. CNC machining however, is able to achieve the necessary precision, tolerances and repeatability that will guarantee a watertight seal, every time.
Look for robust procedures
It’s worth noting that while CNC machining is the best manufacturing method to create watertight underwater housings or enclosures, achieving them in reality relies on the CNC machining company having robust procedures that are consistently followed.
Manufacturing precisely mating components for marine applications takes skilled, experienced machinists, backed up by a series of processes that will ensure repeatable quality. If you’re looking for a CNC machining company that’s up to the job, make sure you ask what methodology, processes, or procedures they use to reassure you that your components are in safe hands.
One of the main areas of risk when it comes to CNC machining for ocean technology is the interface between humans and machines. Human error happens, but robust processes provide checks and solutions to stop errors before they are made.
For example, machining complex shapes with a single setup is one way of reducing human error in machining, as it reduces human intervention.
The above picture shows how engineers at Penta created a clever setup that allowed them to machine three components simultaneously, reducing manual intervention for enhanced accuracy, repeatability and efficiency. You can see a video clip of the machining in action over on our LinkedIn page.
The trouble with 3- and 4-axis machining for subsea components
3- or 4-axis machines can only access certain surfaces, and so components such as a marine technology housing or underwater enclosure will undergo multiple machining ops (operations) – and multiple human interactions. Setting up multiple ops needs exacting precision from the machinist to ensure the component is in the correct position before cutting. This can be achieved through clever fixturing, but there are other ways.
5-axis machining is the best match for marine technology components
The most reliable way of machining for subsea technology is through the use of 5-axis machines, programmed by highly skilled engineers, sometimes alongside clever fixturing like the above example. This way a machine can access every surface of a component, eliminating the need for multiple setups and taking human error out of the picture.
When dealing with exacting quality standards, even a micrometre can make a difference to an underwater housing being successfully water tight, or gradually starting to leak.
Essential quality procedures for any company that machines marine components
Quality procedures are also critical to achieve the pinpoint accuracy that a truly watertight seal needs. First-off inspection by skilled inspectors checks that a machining programme is running correctly, the material is loaded properly, and everything is working as it should. Once the first off has been checked and signed off, the remainder can then be manufactured.
For long runners, checking a set quantity at agreed batch numbers ensures that any tool-wear or other fluctuations within a machining process are being managed, and the machine continues to run within tolerances.
Final inspection of manufacturing then gives the assurance that each component is fully water tight. Certification is usually available for proof of inspection.
Look for a company that has documented machining and inspection procedures that are followed consistently. This will give you the guarantee that every component will achieve the exacting standards required to be corrosion-proof and watertight within marine applications.
Our handy checklist of questions to ask a prospective CNC machining company about its quality procedures is a great place to start. Download it here.
What finishing processes can be used for marine technology?
Depending on the material selected, there will be different finishing processes that are possible. Some will help to improve properties such as corrosion resistance, while others will be primarily around aesthetics.
If your design includes a finishing process, such as anodising, powder coating or iriditing, it’s important to ensure that you consider the necessary machining allowance for all surfaces where marine technology components meet or join together. A layer of material is added in these processes, and it can push a perfectly-fitting set of components into the scrap pile.
Consider too that some finishing processes are more ‘artisanal’ than precision, so it’s best to work with a company with expertise in both CNC machining and finishing to ensure the desired finish is achievable and appropriate for the application.
What next?
If you need a reliable CNC machining company to manufacture components for your marine technology or underwater application, get in touch with Penta.
Find out more about our marine machining service.
Our company is built on core processes, with each area of the business responsible for examining, improving and following their particular processes. We have put these in place to ensure every customer has a consistent, high quality experience.
We often work with designs that have tight tolerances and exacting machining requirements, including those within the marine technology industry, and collaborate closely with a small number of trusted suppliers who provide coatings, anodising or iriditing services that won’t jeopardise seal effectiveness.
Penta’s customers benefit from our innovative manufacturing techniques, advanced machinery and our committed, highly-skilled estimation, preparation and shopfloor engineers who truly care about the work they do.
If you’re looking for a quality and experienced supplier for your marine application, get in touch with my team on 02392 668 334, or email us at