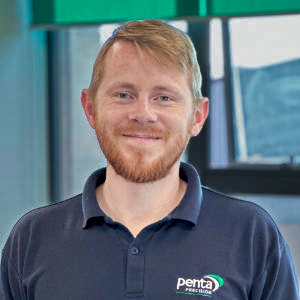
Quality issues in manufacturing often come down to one thing: precision. When you're producing high-spec components for aerospace, medical, or defence industries, even the smallest deviation can create major problems. That’s why more manufacturers are turning to Coordinate Measuring Machines (CMMs) to keep their quality consistent and their processes reliable.
This guide will explore how CMM inspection improves CNC quality control from start to finish. You’ll learn how it boosts accuracy, reduces inspection time, and helps us measure even the most complex part geometries. Whether you’re building prototypes or running full-scale production, our CMMs will give you the confidence that your components meet exacting standards.
What is a CMM?
A Coordinate Measuring Machine (CMM) is a specialist tool used to check whether a part has been manufactured to exact specifications. It uses a probe to scan the surface of a component, either by touch or without contact, to collect precise measurements. These measurements are used to create a 3D digital model that confirms whether the part meets the required tolerances.
At Penta Precision, CMMs help us carry out full 3D inspections across all three axes, X, Y, and Z. Whether we’re checking a simple bracket or a complex medical component, this ensures the final part matches your original CAD file. If you’ve ever asked “what is CMM inspection” or “what is CMM measurement,” it’s this process of digitally verifying every detail before your parts are delivered.
By relying on CMM inspection rather than manual methods, we can detect the smallest deviations before they become problems. This means less risk of rejected parts, improved consistency, and greater peace of mind for you. It’s one of the key reasons customers in aerospace, medical, and defence sectors choose to work with us.
Types of CMMs and Their Uses
Not all CMMs are designed for the same kind of inspection. Each type has specific strengths depending on part size, complexity, and production needs. Understanding these differences helps ensure the right method is used for accurate, consistent results.
Manual CMMs
Manual CMMs are operated by hand and are typically used for simpler geometries or low-volume parts. They're useful in early-stage development or prototyping, where direct control allows for quick, flexible inspection. Accuracy depends on operator expertise, but with skilled handling, they deliver highly reliable measurements.
These systems are commonly paired with fixed or manually indexed probe heads. This allows inspection of individual features, especially on small or straightforward components. While slower than automated methods, they remain a cost-effective solution for certain jobs.
Manual CMMs are well-suited to situations where one-off or short-run parts need close attention. They provide a solid foundation for inspection without the need for full automation. For more complex or repeatable tasks, a CNC CMM may be more appropriate.
CNC (Automated) CMMs
CNC CMMs are fully automated and controlled by inspection software, making them ideal for medium to high-volume production. They follow pre-programmed paths, measuring parts with high speed and repeatability. This reduces variability and ensures consistent quality across multiple batches.
Automated probes can rotate and access difficult features without manual adjustment. These machines are frequently used for aerospace components, tight-tolerance parts, and precision CNC milling applications. Their ability to handle complex geometries makes them essential in high-precision environments.
CNC CMMs also streamline processes like First Article Inspection (FAI), where detailed dimensional verification is required. They can store routines for repeat use, increasing efficiency over time. For projects that require thorough, traceable inspection, they offer significant long-term benefits.
Portable CMMs
Portable CMMs offer flexibility by allowing the measuring device to be brought directly to the part. These include articulated arms or laser scanners, useful for large or immovable components. While slightly less precise than fixed systems, they deliver reliable results in dynamic environments.
They're often used for on-site inspections, large assemblies, or reverse engineering applications. Portable systems make it easier to inspect hard-to-reach areas or features during maintenance and production support. This adaptability helps reduce handling and downtime in time-sensitive projects.
Though not suited for all tolerance levels, portable CMMs offer practical solutions for unique inspection challenges. They are especially useful when space or part size limits access to traditional equipment. When used correctly, they contribute to a streamlined quality control process.
Choosing the Right CMMs
Selecting the right CMM depends on the part's geometry, inspection frequency, and required precision. Bridge and gantry machines suit larger parts and tighter tolerances, while manual systems are more appropriate for low-volume, simpler jobs. Portable CMMs serve best in mobile or space-constrained situations.
The goal is to use the most effective inspection method for the task at hand. This ensures accuracy without adding unnecessary time or cost. The right CMM choice contributes directly to reliable, repeatable results.
Integrated as part of a wider CNC machining inspection process, the correct CMM setup supports consistency, traceability, and confidence in every finished part. It's one of several quality assurance tools used to meet high customer expectations. In precision manufacturing, these decisions play a key role in overall project success.
How CMMs Improve CNC Quality Control
CMMs do more than check dimensions, they play a critical role in maintaining consistent manufacturing quality. By supporting precise measurement, early error detection, and faster verification, they help ensure parts meet exact requirements. Here's how CMM inspection strengthens every stage of the CNC machining process at Penta Precision.
Enhancing Accuracy
CMMs provide micron-level accuracy, far beyond what traditional handheld tools can achieve. This ensures every feature of a part aligns exactly with the original CAD model. It's one of the main reasons why CMMs are standard in industries with strict tolerance requirements.
By eliminating operator subjectivity, they deliver reliable and repeatable results across multiple shifts. CMM inspection software automates each step, reducing variability and boosting trust in the data. This consistency is vital when multiple components must fit together without fail.
CMM software also supports advanced inspection methods like Geometric Dimensioning and Tolerancing (GD&T). This allows not just measurement of size, but also of form, orientation, and positional accuracy. For customers, this means higher assurance that critical features are fully verified.
Reducing Inspection Time
Traditional inspection methods can be time-consuming, especially when parts are complex or high in volume. Coordinate Measuring Machines significantly speed up the process with automated routines and instant data capture. What once took 30 minutes can now be completed in a matter of minutes.
Quicker inspection cycles mean earlier feedback and fewer production delays. Potential issues can be identified and corrected sooner, reducing waste and rework. For customers, that translates into faster lead times and more consistent delivery.
Coordinate Measuring Machines are ideal for batch inspections, allowing you to inspect multiple parts in sequence with minimal input. Inspection routines can be saved and repeated without starting from scratch. That makes them a valuable asset in busy and fast-moving production environments.
Standardising Quality Control
Coordinate Measuring Machines make it easier to standardise inspection routines across teams and facilities. Each part is measured the same way, every time, ensuring consistency regardless of who's running the shift. This is especially important when producing parts for regulated or high-stakes industries.
Digital records created by CMMs provide traceable data that supports audits and quality certifications. For companies working to ISO 9001:2015 standards, this level of documentation is essential. It also helps demonstrate a clear commitment to quality assurance when working with regulated sectors.
Standardisation also makes it easier to scale production or onboard new team members. Familiar software interfaces and programmed routines reduce the training curve. That ensures CMM quality is maintained, even as capacity grows.
Measuring Complex Geometries
Coordinate Measuring Machines are built to handle complex features that traditional tools struggle with. Whether it's curved surfaces, deep recesses, or tight angles, CMMs can inspect them accurately and efficiently. This gives you greater design freedom and supports more advanced engineering.
Scanning probes and non-contact sensors help gather data on surfaces that require high resolution. This includes items like turbine blades, surgical instruments, or multi-surface enclosures. With these tools, manufacturers can confidently validate parts that push the boundaries of design.
Advanced CMMs can also adjust probe angles during inspection to access hidden features. This eliminates the need to reposition the part manually or guess at difficult areas. The result is more complete inspections, and fewer surprises down the line.
Benefits of CMMs in CNC Machining
The advantages of using a Coordinate Measuring Machine go well beyond just improving measurement precision. They help create a smarter, more efficient workflow that supports better outcomes at every stage of production. From saving time to strengthening quality, the impact is tangible.
Using CMMs reduces the likelihood of dimensional errors or unexpected defects. That means fewer rejected parts, fewer production delays, and more dependable results. In competitive industries, this level of reliability builds long-term customer trust.
CMMs also improve efficiency by making inspection faster and more repeatable. Automated routines reduce time spent on manual checks and streamline the entire workflow. This enables tighter turnaround times without compromising quality, additional benefits include:
- Better process control through real-time feedback and measurement data.
- Reduced delays from rework or failed inspections.
- Increased assurance on complex or high-value parts that demand full dimensional traceability.
For businesses requiring precision CNC machining, the consistency that CMMs provide is a key differentiator. They help ensure that every part delivered meets your exacting standards. It's one more way Penta Precision delivers quality you can rely on.
Challenges and Considerations
CMMs are powerful tools, but like any precision equipment, they require the right setup and environment to deliver accurate results. Understanding these factors helps ensure consistent performance and protects the integrity of each inspection. At Penta Precision, we manage these challenges to maintain the high standards our customers expect.
Environmental conditions can affect measurement accuracy if not properly controlled. Factors like temperature fluctuations, vibration, and humidity can interfere with CMM performance. That's why many CMMs are housed in dedicated inspection areas designed for stability and consistency.
Routine calibration is also essential for maintaining long-term precision. Following standards such as ISO 10360 ensures that measurement results remain traceable and compliant. Preventative maintenance helps reduce the risk of downtime or inaccurate readings. Important considerations include:
- Ensuring operators are trained to understand technical drawings and use GD&T effectively.
- Selecting the right probe type based on material, surface finish, and geometry.
- Planning for ongoing support, software updates, and system servicing to maintain performance.
While there are alternatives like vision systems or laser scanners, none offer the full traceability and dimensional verification of a CNC machining inspection process that includes CMMs. That's why CMMs remain the go-to choice for high-precision manufacturing. They provide the clarity and control needed when quality simply can't be left to chance.
Key Takeaways on CMM in CNC Quality Control
CMMs play a crucial role in maintaining the high standards expected in modern CNC machining. They help ensure every component is measured against its design with complete accuracy and repeatability. For customers, this means consistent part quality, fewer delays, and greater peace of mind.
Beyond quality assurance, CMMs contribute to faster approvals and reduced production risk. By identifying issues early and providing reliable inspection data, they help projects stay on track. Whether you're ordering a one-off prototype or a full production run, the results are measurable.
For businesses that depend on precision CNC milling, a robust inspection process is essential, not optional. CMMs offer the traceability and confidence needed to meet demanding specifications. That's why they're such an important part of the way Penta Precision delivers long-term value.