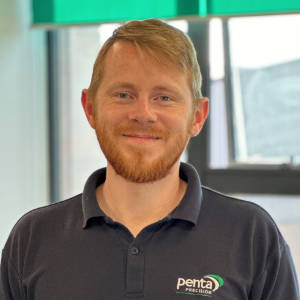
Which Aluminium Alloy Do I Need?
Aluminium is not like stainless steel: there is no one ‘stand out’ grade that is the first choice for medical devices. There is no ‘316L’ of aluminium.
Instead, as a purchaser of medical component machining solutions, you are confronted with a plethora of aluminium grades – any, all or none of which may suit your specific medical application.
To suggest that’s a challenge is an understatement. But it also offers you a great opportunity to improve quality, consistency and savings. How so? Simply this…you won’t be on ‘316L autopilot’ as sometimes occurs in the world of stainless steel medical components.
You won’t sleepwalk into ordering an ‘obvious’ grade of aluminium (that may be more expensive than you need) – because there isn’t one. But these are the grades that you should be looking at…
2014A (L93, L157, L168) – Extremely Strong Aluminium Alloy
The parallel ‘L’ designations for 2014 tell you immediately that you’re dealing with a serious grade of aluminium for aerospace applications:
- L93 plate
- L157 sheet
- L168 bar (the most widely used grade of aluminium in the aerospace industry).
2014 is an extremely strong grade of aluminium, retaining that strength after heat treatment (when it behaves much like low-carbon steel). But that robustness comes at a premium: 2014 is the second-most expensive grade of aluminium after 7075.
2014A is fully heat-treated with a 4-5% copper alloy, adding to its strength. However, the copper reduces ductility and also corrosion resistance. The most common temper (hardness) is T651, which involves solution heat treatment, stress-relief stretching and artificial aging.
Sadly, you cannot anodise 2014 aluminium (and nor is it suitable for welding, brazing and soldering). However, it can be coated with either Iridite NCP or Surtec 650 to help prevent corrosion and provide a surface for painting/powder coating if need be.
It is possible to hard anodise 2014A; this is often done to improve corrosion resistance. If you need colour anodising, we recommend dark colours for superior consistency of finishing.
Ultimately though, if you’re specifying 2014, it’s better for concealed internal components that need to be tough but will not require cosmetic finishing.
Find out more about 2014A aluminium alloy.
7075 (L95) Aluminium – Strong, Refined With Consistent Finishing
7075 is another aerospace-grade aluminium that is available in round bar and plate. It has a higher tensile strength than 2014 and is also manufactured to more exacting metallurgical tolerances – ensuring greater consistency.
7075 is so strong that it is comparable with many steels. It is stronger at sub-zero temperatures (but weaker at very high temperatures).
Strength and other attributes will depend on which temper you specify:
- T6 has the highest strength but the downside is a lower resistance to stress-corrosion cracking
- T73 offers better resistance to stress-corrosion cracking but the trade-off is lower strength
- T76 offers improved exfoliation resistance and slightly superior stress-corrosion resistance to T6 (with some reduction in strength).
However, 7075 is a more refined grade of aluminium when it comes to finishing. For these reasons, 7075 T651 plate is just over 10% more expensive than its 2014 equivalent but it’s worth it. It is an extremely good grade of aluminium that can be anodised, offering a good, consistent finish.
And that matters because anodising is not a precision process like machining. It is – with respect – an artisan process: there are variables that are out of your control; you are at the mercy of electrolysis and chemicals. That is why we entrust our precision-machined components only to very high quality finishing specialists.
Read our technical guide to 7075 aluminium.
6082 (L111 bar, L113 sheet, L114 tube, L115 plate) – Commercial Grade Aluminium
6082 T6 is used for 70% of all aluminium applications. It is a popular commercial grade that is good value and widely available.
6082 has aerospace designations – so it offers reliability and consistency – and yet it is significantly more cost effective than most other grades of aluminium.
That makes it the perfect choice for most commercial applications – hence its popularity.
6082 is good for high-stress and structural applications, such as bridges or trusses. Aside from its aerospace/defence credentials, it is popular among industries including the automotive and transport sectors, architecture and chemical production.
All aluminium is good to machine but particularly 6082. Off-the-shelf cutters can be used – saving time and money – and there is less tool wear. That means faster speeds and feeds, reduced production cycles and quicker turnaround times.
If you're sourcing components made from this material, working with a specialist in precision aluminium CNC machining services can help maximise efficiency and surface quality right from the outset.
6082 is known as ‘the dirty aluminium’ because it is less pure than other grades – but its impure metallurgical composition means that it anodises quite well. Options include sulphuric or hard anodise (natural or colour in both cases), along with Iridite NCP or Surtec 650 for protection from corrosion.
Availability of 6082 is very good, as you might expect for a grade this popular. Plate, round bar and flat bar are usually held in stock. This speeds up deliveries.
There might not be a ‘316L of aluminium’ but 6082 has a lot going for it.
Read our 6082 machining guide for more information – especially the Technical Properties and Typical Chemical Composition tabs.
5083 Marine-Grade Aluminium – Resistant To Chemicals
5083 is a known as a marine-grade aluminium because of its good resistance to seawater. Its anti-corrosion properties also make it an excellent choice for applications involving industrial chemicals.
It does not have an aerospace ‘L’ grading and is not as strong as some other grades but it is still very strong after welding. (Though it is not recommended for applications where temperatures are likely to exceed 65°C).
5083 has the highest strength of the non-heat treatable aluminium alloys. The fact that it is specified for some defence, petrochemical and nuclear applications speaks volumes about its dependability.
This grade is cast tooling plate – so it has a uniform microstructure – making it a very consistent grade of aluminium to machine. Internal stresses are low.
Cast tooling plate is supplied to a flatness tolerance, offering significant benefits in applications where consistency of flatness may be a challenge. The two main faces are plough ground and then polycoated to give a better and more consistent finish.
5083 is a good grade for anodising (but only with a commercial finish – not an aesthetic one). It is also the most cost-effective of all the grades we list here: around a third cheaper than top-rated 7075 T651.
But there is a downside to 5083. Fine detail work – such as screw threads – can be weak. You will need to strengthen fragile threads with wire inserts or helicoils.
Read our 5083 machining guide for more information.
6061 Aluminium – An Increasingly Popular Grade
6061 is better known in North America than it is in Europe. But this medium-to-high-strength alloy is becoming increasingly popular on this side of the Atlantic too. The UK equivalent is 6082.
So why would you specify 6061 instead of 6082? The short answer is that – for a number of applications – you wouldn’t:
- 6082 has a higher tensile strength (340 MPa vs 6061’s 260 minimum MPa)
- 6082 has a lower copper content – maximum 0.10 vs 6061’s 0.80-1.20 – and so has a better resistance to corrosion.
But there are differences, notably in the processing methods for each grade – and this matters:
- 6061 is cold-processed – it coats well and is suitable for applications with high oxidising requirements
- 6082 aluminium sheet is a heat-treated alloy with medium strength and good operability after annealing.
There is also the question of price. 6061 can be 30% more expensive than 6082 so you would need a very good technical reason to justify that extra expenditure. 6061 is also less readily available.
Compare the two alloys in more detail:
6063 Aluminium Alloy For Extrusions
6063 ‘architectural alloy’ can be heat treated. It is medium strength and has high resistance to corrosion. This grade offers good surface finishing and electrical conductivity – making it easy to anodise.
It is a good grade for extrusions. Purchasers will often specify 6063 for building and construction applications – such as window frames and balustrading – but it can also be used for heatsinks, tubes and piping.
6063 is worth considering if you want a good aesthetically pleasing finish (but stronger grades are available).
Read our technical guide to 6063 aluminium.
Get Penta Involved
Aluminium is always an excellent material to machine – much easier than plastic. Few grades of aluminium create any technical issues when it comes to machining.
However, that is no reason to be complacent when specifying the right grade of aluminium for your application(s). Seemingly subtle variations in alloys’ metallurgical and technical properties can make a difference to the outcome of your project.
So it pays to get expert technical advice: get Penta involved.
Penta Precision is ISO 9001:2015 accredited for quality assurance. Our experienced engineers can alert you to potential design and engineering issues before they become costly and stressful.
Depend on Penta to maintain quality and consistency through validated processes:
- We communicate well
- We take care at each stage
- Our service is consistent.