The Sweet Spot or Radical-Centre of CNC Machining, Automation and Lean
31st Jan 2025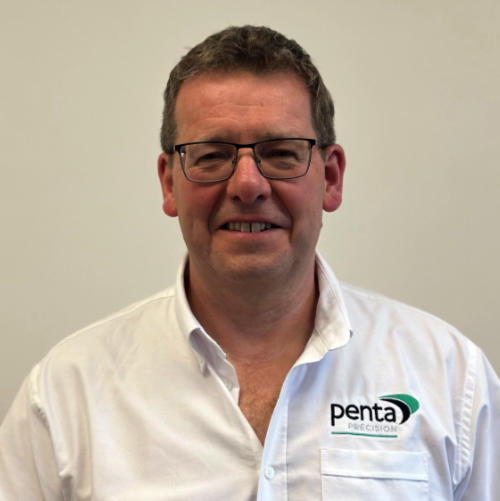
Finding the Radical Centre
What if the future of CNC machining isn't about choosing between extremes like automation versus lean practices or cost versus capability? Instead, it's about finding the right balance. Imagine a tightrope walker expertly managing precision and momentum while focused on the goal. This is the challenge and opportunity we face today.
As engineers and industry professionals, you're seeking solutions that provide precision, reliability, and value simultaneously. At Penta Precision, we have spent decades navigating these demands and have discovered the "radical centre," where cutting-edge automation meets lean manufacturing. This intersection transforms production, customer service, scalability, and innovation.
Recently, during a visit to Mills CNC, a leader in advanced machining solutions, our team witnessed this balance firsthand. We experienced a synergy that combines efficient technology with ingenious lean practices. This journey is reshaping our perspective on CNC machining, and we are excited to share it with you.
Automation Advancements in CNC Milling – Palletisation vs. Robot Tending
Our recent visit to Mills CNC was like stepping into a glimpse of CNC machining’s future. Among the sleek machines and humming operations, two standout technologies caught our attention: the DN Solutions 24-pallet, 5-axis machining centre and a newly premiered 30-pallet retrofit automation solution. Both were undeniably impressive, but what struck us most was how these technologies could redefine efficiency.
Palletisation: A Lean Champion
For us, palletisation isn’t just another tool in the automation toolbox. It’s a game-changer. Imagine running a marathon where every step is perfectly measured, eliminating wasted energy and ensuring maximum endurance. That’s what palletisation does for CNC milling. It integrates seamlessly with lean principles, especially the Single Minute Exchange of Die (SMED) technique, which minimises downtime by converting internal operations into external ones.
During our exploration, we saw how palletisation allowed nearly every setup operation (tool changes, component positioning, and work holding adjustments) to happen in parallel with active production. The result? Machines kept running, schedules stayed intact, and accuracy soared. Even first-off inspection did not affect the production flow, the cell just continued to work the schedule, whilst the inspection happened off-line. In fact, only non-standard tool length measurements and confirmation interrupted the workflow, a stark contrast to traditional setups.
The Palletisation vs. Robot Tending Debate
While robot tending has its merits, it comes with lean principle issues. Before the robot can even get to work, every element (jaws, grippers, work holding fixtures, billet trays) must be proven and consistent. It’s like assembling a jigsaw challenging puzzle, time-consuming and prone to delays. All the time the robot and machine tool capital investment patiently wait to commence what they are best at, when set, working the schedule. Palletisation, on the other hand, doesn’t need to wait for perfected jigsaw puzzle. It thrives in real-world manufacturing environments.
At Mills, we saw a 30-pallet solution that married flexibility with capacity, all at a price point rivalling comprehensive robot tending systems. It was a testament to how automation can be both sophisticated and accessible without compromising on the core principles of lean.
What This Means?
Palletisation isn’t just about reducing cycle times. It’s about ensuring predictable, repeatable outcomes that deliver for your bottom line. It’s a way to future-proof operations while enhancing customer service through faster, more reliable production.
This isn’t just a shift in technology. It’s a shift in mindset. By focusing on where automation and lean principles overlap, companies like Penta Precision together with its investments in Matsuura’s MAM72 range of machines, are finding smarter ways to deliver precision and value without compromise.
The Power of Palletisation and Its Synergy with Lean
Palletisation is more than a clever setup strategy. It’s a philosophy that aligns perfectly with lean manufacturing, driving efficiency while eliminating waste. At Penta Precision, we’ve seen firsthand how this approach transforms operations, enhancing both output and customer satisfaction.
The Lean Connection
In lean manufacturing, the goal is simple: remove waste and increase adding value for the customer. One of the most powerful tools in this arsenal is SMED (Single Minute Exchange of Die). SMED emphasises minimising machine downtime by moving setup tasks from internal (when the machine is stopped) to external (performed while the machine runs).
Palletisation takes SMED to the next level. With standardised toolsets and clever scheduling, nearly all internal setup tasks can be externalised. The machine doesn’t pause for work holding changes or tool alignments; instead, it powers through, delivering consistent, high-quality components.
The only interruptions? Tool length measurements and confirmation for non-standard setups, and of course essential machine preventative maintenance servicing. Palletisation ensures the machine runs while the team perfects the next task, turning downtime into productivity.
A Real-World Example
During our operations, with our proven Matsuura MAM72-35V, we’ve experienced the remarkable impact of this approach. By using palletisation, we achieve 90 to 95% 24/7 production, week on week, without sacrificing accuracy or quality. Lean principles like SMED allow us to switch between works orders effortlessly, in a high work mix environment, ensuring that every part meets specifications while delivering the schedule.
This isn’t just about hitting targets. It was about delivering peace of mind to our customer. They know their orders are in capable hands because our process is optimised for reliability and speed.
Palletisation vs. Robot Tending: An Efficiency Comparison
Here’s where palletisation truly shines. In robot-tended setups, you face a cascade of pre-production tasks. Every gripper, jaw and tray must be carefully adjusted and tested before the robot can even begin. This delays productivity, leaving the machine idle (and robot), the investments sit unused.
With palletisation, however, the focus shifts to maximising uptime. The setup and prove-out for work-holding happen independently, allowing production to continue uninterrupted. This approach not only accelerates delivery but also reduces overall costs, creating a win-win for both manufacturers and customers.
Why It Matters?
Understanding the impact of palletisation is crucial, it offers more than efficiency; it guarantees consistent results at a competitive price. By integrating palletisation into operations, manufacturers can better meet the growing demands for flexibility and precision in today’s market.
This isn’t just about staying ahead of the curve. It’s about setting a new standard for what’s possible in CNC machining. Palletisation, when paired with lean principles, paves the way for smarter, more scalable production that benefits everyone in the supply chain.
The Automation Dilemma in CNC Turning
While palletisation has proven to be a game-changer in CNC milling for both low to high volume milling, the road to seamless automation in CNC turning is less clear. For high-volume production, automation is well-established, traditional systems handle repetitive tasks efficiently, offering consistency and cost-effectiveness. Bar feeders, twin spindle, twin turret formats, parts catchers and take off conveyors have been commonplace for bar work for decades. Gantry loaders, robotic tending, B axis heads combined with extended tooling carousels solutions for medium to high volume billet work are growing in application and extend unmanned running, providing predictable outcomes for long runs of standardised parts.
However, as we step into low-volume, highly customised componentry, the limitations of current automation solutions become apparent. The complexity of work holding setups, diverse part geometries, differing materials and the need for frequent changes demand a level of adaptability that today’s systems often struggle to match. Skilled CNC programmers and setters remain indispensable, bringing intuition and expertise to tasks that robots and AI cannot currently accomplish.
The Search for Solutions
Major machine tool manufacturers are undoubtedly grappling with this challenge. The advent of B-axis turning centres and extended tool carousels represents one step forward, offering greater flexibility in machining complex geometries.
However, a broader leap is needed. Could we see innovations like automated chuck-changing systems or multi-functional spindles that seamlessly switch between bar and billet work? These advancements would transform low volume turning, bringing it closer to the efficiency levels seen in milling. For low volume, high mix billet turn-mill applications, will the likes of the Matsuura Cublex series of palletised automation start to win big? Possibly with additional robot tending loading for lower run time pallets?
Balancing Innovation and Practicality
There’s a critical question here: are these advancements worth the investment, or do they fall into the trap of “overprocessing” the technology? Lean principles remind us that creating systems more complex than necessary often leads to diminishing returns.
Perhaps the solution lies in a hybrid approach, where automation handles repetitive tasks while skilled operators focus on intricate setups. This blend of human expertise and machine efficiency could represent the “radical centre” of CNC turning—a balance between tradition and innovation.
The Role of Lean Principles in Automation Success
As we delve deeper into the interplay of CNC machining, automation, and lean principles, one recurring theme emerges: the pursuit of efficiency without compromise. Lean manufacturing methodologies, particularly SMED offer a framework to unlock the full potential of automation while reducing waste and improving customer outcomes.
Palletisation and SMED: A Perfect Synergy
At Penta Precision, we’ve seen firsthand how palletisation revolutionises efficiency. By allowing nearly all internal setup operations (those requiring the machine to be stopped) to shift to external operations (performed while the machine is running), palletisation aligns perfectly with the principles of SMED.
Consider this analogy: palletisation is like prepping ingredients for a meal before the guests arrive. When dinner time comes, everything is ready to go, so you can focus on cooking instead of scrambling to chop, measure or gather. Similarly, in CNC machining, palletisation ensures that setups like work holding changes, tool swaps, and fixture alignments occur external to the production cycle, the schedule keeps being processed with exceedingly limited “internal” production disruptions.
The results are significant. Only spindle tool length measurements for planned replacement of standard tools and non-standard tools disrupt the production schedule. Even first-off inspections are completed as production continues, as long as these steps are conducted with the right workflows in place.
Automation vs. Waste: Addressing Overprocessing
Automation, when done right, eliminates waste. But what happens when it overshoots the mark? One form of waste in lean thinking is overprocessing - investing resources into exceeding the customer’s requirements or the needs of the application.
Let’s look at robot-tending solutions. While they offer incredible capabilities, the setup process can be time-consuming and resource intensive. Robots must be programmed to handle grippers, components, trays, component grids and billets - all of which must be proved to be consistent and robust before production begins. During this time, the machine tool itself, along with the substantial investment in automation, sits idle, not involved in productive work, waiting for the green light.
In contrast, the combination of palletisation and standardised tooling minimises these inefficiencies. By simplifying the transition between setups, it accelerates time to production and ensures machines spend more time doing what they’re meant to do: machining.
Standardisation: The Secret Ingredient
Standardised toolsets amplify the benefits of both palletisation and lean practices. When tools, fixtures, and processes are predictable, they require fewer adjustments, reducing variability and setup times. This approach extends the principles of SMED and keeps machines running smoothly with minimal interruptions.
Imagine a high-precision watchmaker. Each gear, spring, and component fits seamlessly because of meticulous planning and standardisation. Similarly, in CNC machining, standardisation ensures that every setup is a perfect fit, whether it’s a one-off prototype or a batch of 500 parts, or more.
Customer Benefits: A Win-Win Scenario
Ultimately, the goal of combining lean principles with advanced automation is to deliver tangible value to customers. Reduced lead times, enhanced repeatability, and consistent quality are just a few of the benefits. At Penta Precision, we’ve witnessed how these improvements translate to better service, enabling us to meet tight deadlines and deliver components that exceed expectations.
The Quest for Flexible Automation
The industry is grappling with this challenge. R&D teams at major machine tool manufacturers are exploring ways to make automation more adaptable for turning operations. Features like B-axis capability and extended tooling carousels are in place.
However, fully automating these processes remains an uphill battle. For instance, automating the transition in spindle liners, from bar work to billet handling and back again requires sophisticated technology. Add to this the precision required for tasks like aligning sub-spindles or ensuring chucking accuracy, and it becomes clear why low volume turning relies heavily on skilled human operators.
Innovation vs. Practicality
The pursuit of cutting-edge solutions often walks a fine line between innovation and overprocessing. Could the development of humanoid robotics, like Tesla’s Optimus or Boston Dynamics' Atlas, offer solutions? These robots are designed to replicate human dexterity and adaptability, but their current applications lean more toward warehousing, bomb disposal, or high-risk environments rather than machining.
The investment required to bring such advanced robotics into CNC turning might outweigh the practical benefits for many manufacturers. Yet, like Formula 1’s influence on consumer car technology, these high-end robotic developments could trickle down, offering more accessible solutions in the future.
A Future with Skilled Operators
Given the current state of automation in CNC turning, skilled human operators remain indispensable. Their ability to adapt to varying production demands and troubleshoot complex setups ensures consistent output, particularly in low-to-medium batch production. This highlights a paradox: while automation is advancing, the demand for experienced CNC programmer-setter-turners remains consistent.
The Role of Robotics and AI in Manufacturing
As we explore the potential of automation in CNC machining, it’s impossible to ignore the advancements in robotics and artificial intelligence (AI). From humanoid robots like Tesla's Optimus to Boston Dynamics' Atlas, the industry is witnessing remarkable strides in robotics technology. Yet, the big question remains: how do these developments fit into the world of CNC machining?
The Pursuit of Human-Like Robotics
The vision behind humanoid robots is ambitious: to replicate human dexterity, problem-solving, and adaptability. These capabilities could, in theory, transform manufacturing. Imagine a robot capable of changing a chuck, adjusting a spindle liner, or setting up a machine with the finesse of a seasoned CNC operator.
However, such capabilities come with significant challenges. The technology required to achieve human-level manipulation and judgment demands immense resources. Consider Tesla’s investment in Optimus: its design is geared toward repetitive tasks, like material handling or assembly. For more intricate work, like CNC turning, the complexity of programming and hardware rises exponentially.
Where Robotics Excel Today
While humanoid robots are a long-term vision, more immediate applications of robotics are already reshaping manufacturing. In high-volume production, robotic arms and AGVs (Automated Guided Vehicles) streamline workflows by automating material movement and part handling. Companies like Amazon and Ocado demonstrate how robotics can deliver precision and efficiency at scale.
For CNC machining, palletised automation remains the frontrunner. It combines robotics with proven manufacturing practices to achieve outstanding results in milling. The flexibility and cost-effectiveness of systems like the 30-pallet automation solution from Mills CNC Automation highlight this synergy.
The Debate on Overprocessing
Introducing advanced robotics into CNC machining raises questions about overprocessing. Do we need machines that mimic human capabilities, or should we focus on optimising current systems? Lean principles caution against adding complexity for complexity’s sake. Instead, the goal should be solutions that align with customer requirements while eliminating waste.
Take, for example, the stark contrast between the intricate capabilities of Boston Dynamics’ Atlas and the straightforward efficiency of a palletised milling system. While the former represents technological marvels, the latter addresses specific industry needs directly and effectively.
Balancing Innovation with Practicality
For manufacturers like Penta Precision, the focus must remain on solutions that deliver tangible benefits. While it’s exciting to imagine a future where robots handle every aspect of machining, the industry needs to strike a balance: integrating automation where it enhances productivity without losing sight of practical, cost-effective improvements.
The Takeaway
Robotics and AI hold immense potential for CNC machining, but their role must be carefully considered. As the industry advances, the key will be to adopt technologies that enhance flexibility, efficiency, and quality without falling into the trap of over-engineering.
Finding the Radical Centre
The CNC machining industry is at a pivotal intersection of automation, lean principles, and robotics, creating a unique space for innovation that meets practical needs. At Penta Precision, we've experienced how palletisation in CNC milling has streamlined our workflows, enhancing machine utilisation, accuracy, and delivery through the integration of lean methodologies and flexible automation.
However, challenges persist, especially in CNC turning, where automation for small and medium batches is still developing. While robotics and AI present exciting opportunities, they must be guided by lean thinking to avoid overcomplication. The key questions remain: Are we addressing real needs, or are we overprocessing? Are we investing wisely in technologies that align with market demands?
Moving forward, manufacturers must balance ambition with practicality. Like Formula 1 innovations transitioning to the mainstream, the CNC industry will shape future technologies and practices.
It’s no wonder that Matsuura’s proven MAM72 technology is leading the charge in high mix CNC milling automation, others are following in their path.
Higher volume CNC turning automation is well established. Is Matsuura’s Cublex solution the first insight into how lower volume, high mix CNC turning automation will develop? How can it be further enhanced to process lower run time, low volume, high mix workflows? Afterall, it’s that persistent 24/7 operation that drives down the piece part cost, all performed in a repeatable, high accuracy environment.
As we navigate the next 25 years of industry evolution, Penta Precision is committed to staying at the forefront of these advancements. We’re not just adopting the tools of the future; we’re helping shape them in a way that serves our customers and the broader CNC machining community.