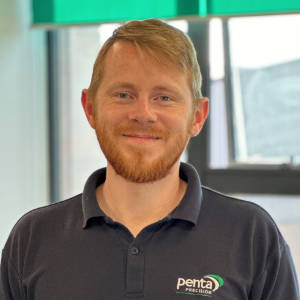
Right Plastic, Right Machining Partner
Plastics can be harder to machine than metals: they can be less forgiving. Machining plastics requires specialist expertise – the kind that comes only with years of experience.
But that’s just half the battle. Not every plastics machining specialist has the experience needed to meet the stringent requirements of medical equipment OEMs.
Choosing the right machining partner for medical applications is vital to ensure quality, consistency, validated processes and traceability of materials.
Key Questions To Ask When Specifying Plastics for Medical Devices
There is no one perfect plastic for medical manufacturing. The wide range of requirements in the healthcare sector can make specifying the best plastic at the right price highly challenging:
- Does the plastic have to be biocompatible with skin tissues and blood? Will it meet USP certification standards?
- Will it meet ISO 10993 standards with regard to cytotoxity (toxicity to cells), growth inhibition, haemolysis (rupture/destruction of red blood cells), chemical analysis/’fingerprinting’ and biological-toxicological evaluation?
- Can the plastic withstand high temperature sterilisation? Is it steam autoclavable? Will it meet the DIN EN 285 standard (exposure to pure saturated water vapour at 134 °C for at least three minutes)? How many sterilisation cycles can the plastic withstand before it starts to degrade?
- Will the plastic need to be X-ray opaque so it shows up during radiography procedures? Most plastics are not ‘visible’ to X-rays – increasing the risk of ‘never event’ medical negligence if they don’t show up during scanning.
- Are high tolerances required? Plastic may have a reputation of being waterproof but the reality is that many types absorb minute quantities of water, affecting their dimensional stability.
- Will the plastic need to maintain precise dimensional stability in higher temperatures?
These are just a few examples of the questions you need to think about when it comes to plastics for medical applications.
Others include strength/robustness, UV stability, the overall finish (for easy cleaning and sterilisation) and ergonomics: how comfortable will the plastic be to hold and handle if required?
And that is before you get the crucial question of cost. There can be huge differences in the price of what can initially appear to be very similar plastics.
Which Medical Plastics Are Best For My Application?
Some specifiers can all too easily default to ‘ABS autopilot’. This tough and ubiquitous ‘go-to’ plastic might be a good all-rounder but there are better choices for the demanding requirements of medical manufacturing.
PEEK (Polyetheretherketone)
PEEK is a strong, high-performance engineering thermoplastic with a very high resistance to chemicals. It offers good stiffness thanks to its resistance to heat (up to 170 °C) and excellent dimensional stability because it is resistant to steam, water and sea water.
PEEK is a popular plastic for medical instrument parts because it is suitable for sterilisation. It can also cope well with tough environments.
This robust and resilient plastic is very good to machine because it’s so stable (though it tends to wear out tools faster). But despite its strength, PEEK can still be prone to the odd chip. Bear that in mind if you are specifying thin and fragile components.
Furthermore, PEEK is expensive – 10 times the price of Delrin, acetal or Nylon. So it tends to be a choice for higher end equipment in the medical sector where applications are more demanding. Specifying a trademarked PEEK – such as Victrex 450G – offers traceability for greater peace of mind.
PPSU (Polyphenylsulfone)
PPSU is expensive like PEEK but is less commonly used because it is more difficult to obtain.
It has better impact strength and chemical resistance than PSU (Polysulfone) and PES (Polyethersulfone) – plus a number of other properties that make it ideal for medical applications:
- high operating temperature (up to 180 °C) – it is capable of withstanding superheated steam during sterilisation
- resistant to disinfectants and detergents
- good resistance to X-rays and gamma rays
- dielectric – a good electrical insulator.
PPS (Polyphenylene Sulfide) is very similar to PPSU in terms of density and heat capacity and has a different strength/weight ratio (PPS: 63 to 136 kN-m/kg PPSU: 51 to 82kN-m/kg).
Find out more here about machining PPS
PEI (Polyetherimide)
PEI is extremely expensive. It’s resistant to heat (180 °C) but can be quite brittle. It machines like PC (Polycarbonate) but is more brittle than PEEK.
Like other high-performance plastics, PEI offers high strength, rigidity and dimensional stability along with very good resistance to hydrolysis so it will withstand a punishing regime of steam sterilisation.
PEI also offers high creep resistance; it is less prone to deforming permanently when subjected to constant stress.
So how brittle is PEI during machining? It has reasonable impact resistance: it won’t break if you drop it. But it requires expert machining skills to avoid breaking a brittle edge. That means a slow approach at the start of a cut and equal care at the end.
PEI Ultem resists cracking when exposed to alcohols, acids, automotive/aircraft fluids and aliphatic hydrocarbons. Once again PEI Ultem (registered trademark) is commonly specified in applications where traceability is a necessity.
Find out more here about machining PEI
PP (Polypropylene)
Medical-grade PP - Polypropylene is stable in high heat environments (such as repeated steam sterilisation). It offers low residual stress and good dimensional stability.
In theory, it is easy to machine. But in practice the swarf can bind up on tools leading to in process program stops for clearing The use of high speed steel (HSS) cutters that have a sharper edge than carbide can assist. Again it requires skill; smaller cuts to reduce the heat going into the material.
Find out more here about machining Polypropylene
POM (Polyoxymethylene), Acetal, Delrin
Medical-grade POM is resistant to a range of cleaning products, disinfectants, solvents and hot steam sterilisation.
POM offers excellent value because it is a fraction of the price of expensive plastics such as PPSU, PEEK and PEI.
Medical sector manufacturers specify POM for applications including surgical instruments and sizing trials for knee, hip and shoulder replacements.
POM’s properties include:
- high resistance to chemicals (notably alkalis, fuels and solvents)
- high strength and hardness
- good dimensional stability
- low moisture absorption.
POM thermoplastics are also known by the name Acetal:
- Acetal C – a copolymer made by combining more than one type of monomer (molecule)
- Acetal H – a homopolymer created with a single monomer.
Acetal C (pH 4-13) has better chemical resistance than Acetal H (pH 4-9) and higher hydrolysis resistance (up to 85 °C). But Acetal H has 15% higher strength/stiffness and 10% higher creep resistance.
Many customers requiring Acetal H for medical applications ask for DuPont’s trademarked product Delrin because it can be easily traced back to the original source for quality control purposes.
Delrin is “the ideal material in parts designed to replace metal” in high-load mechanical applications such as healthcare delivery devices, safety restraints and gears. Its high strength, resilience and creep resistance make it a key plastic for creating lighter and thinner parts.
Is DuPont’s trademarked Delrin much more expensive than generic Acetal? No – so it is well worth specifying it by name for dependability and traceability.
Find out more here about machining Acetal/POM
PTFE (Polytetrafluroethylene)
PTFE is best known as a non-stick coating but is often used as a graft material in surgery. It is also used to coat surgical instruments and medical components (such as catheters, guidewires and implantables).
The good news is that PTFE is:
- the only polymer with zero water absorption
- strong and versatile
- low friction
- heat- and cold-resistant – it can be used between -200 °C and +200 °C (melting point 327 °C)
- resistant to electricity, offering good insulation.
On the downside, PTFE is costly (though not as expensive as PPSU, PEEK and PEI) and it is problematic and challenging to machine (and deburr) if you are not used to it. But our engineers have the expertise needed to maintain consistent quality when machining PTFE to fine tolerances.
Find out more here about machining PTFE
Higher Quality, Greater Consistency
Penta Precision has a reputation as a specialist in the machining of all grades of plastics including various types of plastic used in medical devices. We gained that reputation through years of care, consistency and good communications with our customers.
Machining plastic requires more much care than metal. Plastics tend to flex away from the tool because they are less rigid (then bounce back afterwards). Greater care must be taken during clamping. Plastics can also ‘grab’ at the tool during machining and are more likely to gum it up with swarf.
Experience and expertise can overcome all these pitfalls.
Plastic does not require finishing in the same way that metal does. But that doesn’t stop us from obsessing about the finish though. Especially deburring.
Greater Buying Power Gives You Better Value
As you have read, there are significantly more cost-effective alternatives to specifying PEEK. Acetal is at least a decimal place cheaper than PEEK as a raw material. Acetal is also easier to machine – saving us (and therefore you) time and money.
But whichever plastic(s) you specify, you can depend on Penta’s buying power. We can buy plastics at better rates than a lot of materials suppliers! And we pass those savings on to you.
Get Penta Involved
It pays to get Penta involved for your medical plastics machining needs. We will solve the machining design and engineering issues you didn’t know you had – before they become expensive problems.
Benefit from Penta’s three ‘C’s:
• We communicate well
• We take care at each stage
• Our service is consistent.
Penta offers ISO 9001:2015 quality assurance and validated processes. You can also learn more about our broader plastic machining capabilities to see how we support a wide range of industries beyond the medical sector.