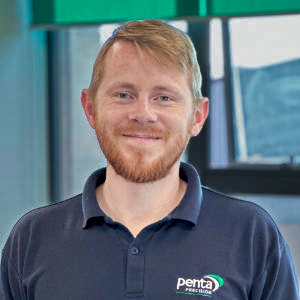
Tolerancing errors are one of the most common reasons for quality issues in manufacturing. In CNC machining, even small tolerance mistakes can lead to part failures, rework, or costly delays. If you work with CNC-machined components, understanding how different types of tolerance work could save you both time and money.
Unilateral and bilateral tolerances control how much variation is allowed when manufacturing a part. The way these tolerances are applied affects the part's fit, function, and manufacturability. Understanding the difference between bilateral vs unilateral tolerance helps ensure parts are produced accurately and perform as intended.
Unilateral Tolerance
If you're wondering "What is a unilateral tolerance?", it is a one-directional limit applied to a part's dimensions. It restricts variation to only one side of the nominal value, either above or below, but never both. This method is especially useful when strict control is needed to protect function or fit.
Characteristics
A unilateral tolerance allows variation in only one direction from the target dimension. For example, a part may be allowed to be up to 0.1 mm smaller, but not any larger. This ensures that parts stay within critical limits where excess size or material could cause failure.
The tolerance is typically expressed as +0.00/-0.10 or -0.00/+0.10, depending on the requirement. It's commonly used when a component must not exceed a maximum or fall below a minimum. Because only one direction is monitored, it can simplify both design and inspection processes.
This directional control helps improve reliability and consistency across mating components. It's ideal in cases where one part must move freely within another without the risk of being too tight. For example, a shaft intended to slide into a hole without resistance would often be produced using unilateral tolerance.
Applications & Examples
Unilateral tolerance is best suited to components where a precise clearance is essential. A common unilateral tolerance example is a press-fit shaft or pin that must never exceed a given diameter. In these cases, the shaft may be undersized slightly to ensure a proper fit, but cannot be oversized.
This approach is often used in sectors like aerospace, medical, and automotive manufacturing. It's especially useful in parts that require consistent assembly or support load without deformation. Where materials may expand due to heat or stress, unilateral control helps preserve critical dimensions.
Because only one limit needs to be verified, inspections are faster and easier to manage. This can lower production costs and reduce scrap or rework from oversizing errors. For tightly fitted assemblies, it provides a reliable way to maintain function without compromising safety or quality.
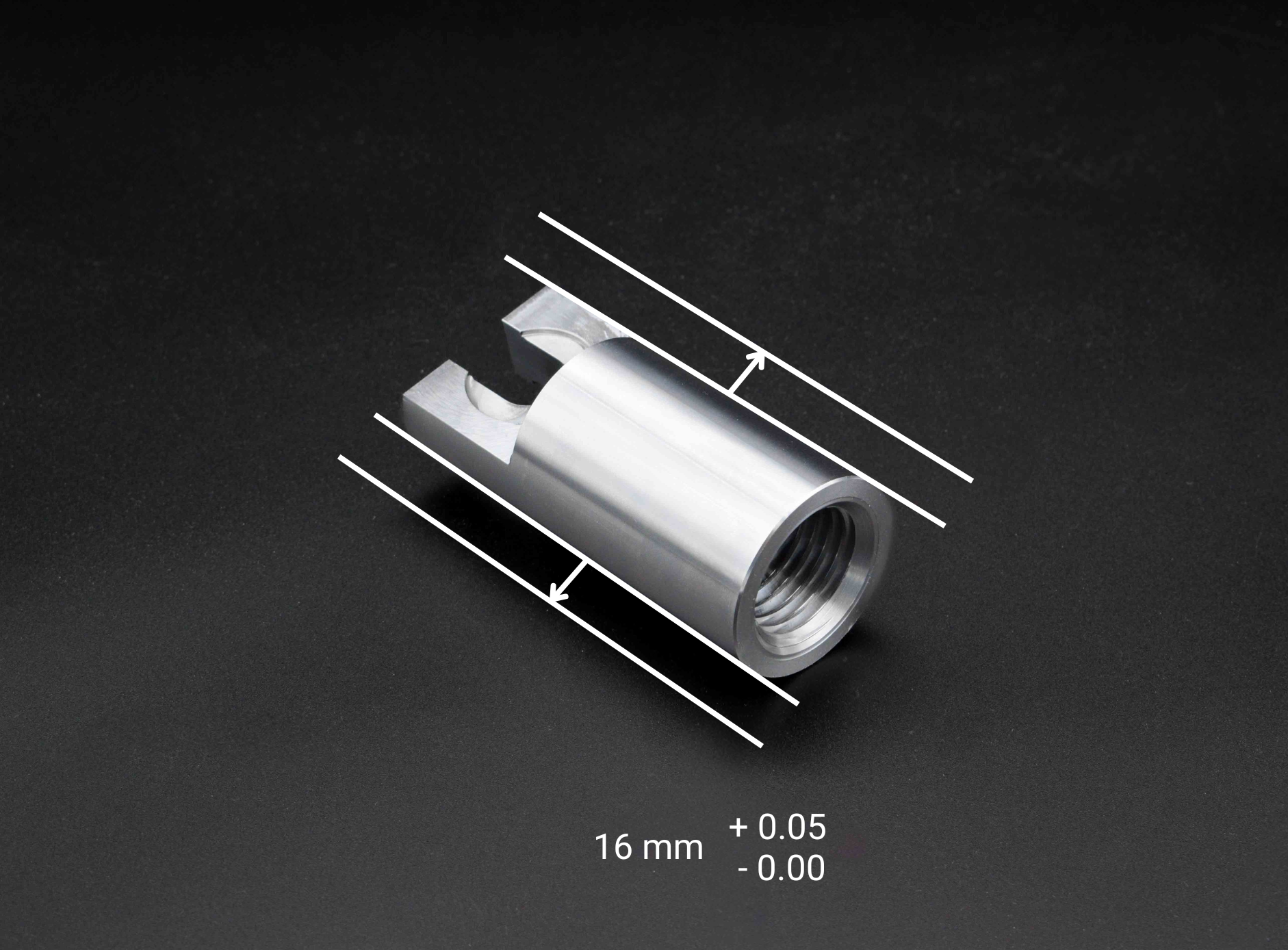
Bilateral Tolerance
If you're questioning "What is a bilateral tolerance?" it allows part dimensions to vary both above and below the nominal value. This provides greater flexibility during manufacturing and inspection without sacrificing functionality. It's commonly applied to non-critical or aesthetic parts where small dimensional shifts are acceptable.
Characteristics
A bilateral tolerance forms a tolerance zone that extends in both directions from the nominal size. For instance, a part specified as 25 mm ± 0.2 mm can range from 24.8 mm to 25.2 mm. This range helps accommodate typical machining variation while keeping the part within acceptable limits.
Typically, the tolerance is evenly distributed, but it can be adjusted to favour one side. This is known as unequally disposed tolerance and is useful when one direction allows for more deviation than the other. It's a flexible approach when design intent permits more variation on one side of the nominal dimension.
Bilateral tolerances are easy to interpret and widely accepted in standard manufacturing workflows. They are suitable for features that don't have tight mating or movement requirements. This makes them ideal for items like mounting plates, enclosures, or outer covers.
Applications & Examples
A common bilateral tolerance example would be a housing cover that can be slightly larger or smaller without affecting assembly. These features don't require high-precision alignment or direct mechanical engagement. Allowing for variation in both directions helps reduce cost and improve production speed.
You'll frequently see bilateral tolerances on non-mating components and cosmetic surfaces. They're especially helpful in high-volume manufacturing, where a broader tolerance window leads to higher yield. Examples include brackets, spacers, and faceplates.
Bilateral tolerance is also well-suited to components made from plastics or composites. These materials may expand or shrink unpredictably, and the two-way flexibility helps maintain dimensional integrity. This approach strikes a balance between manufacturability and reliable function.
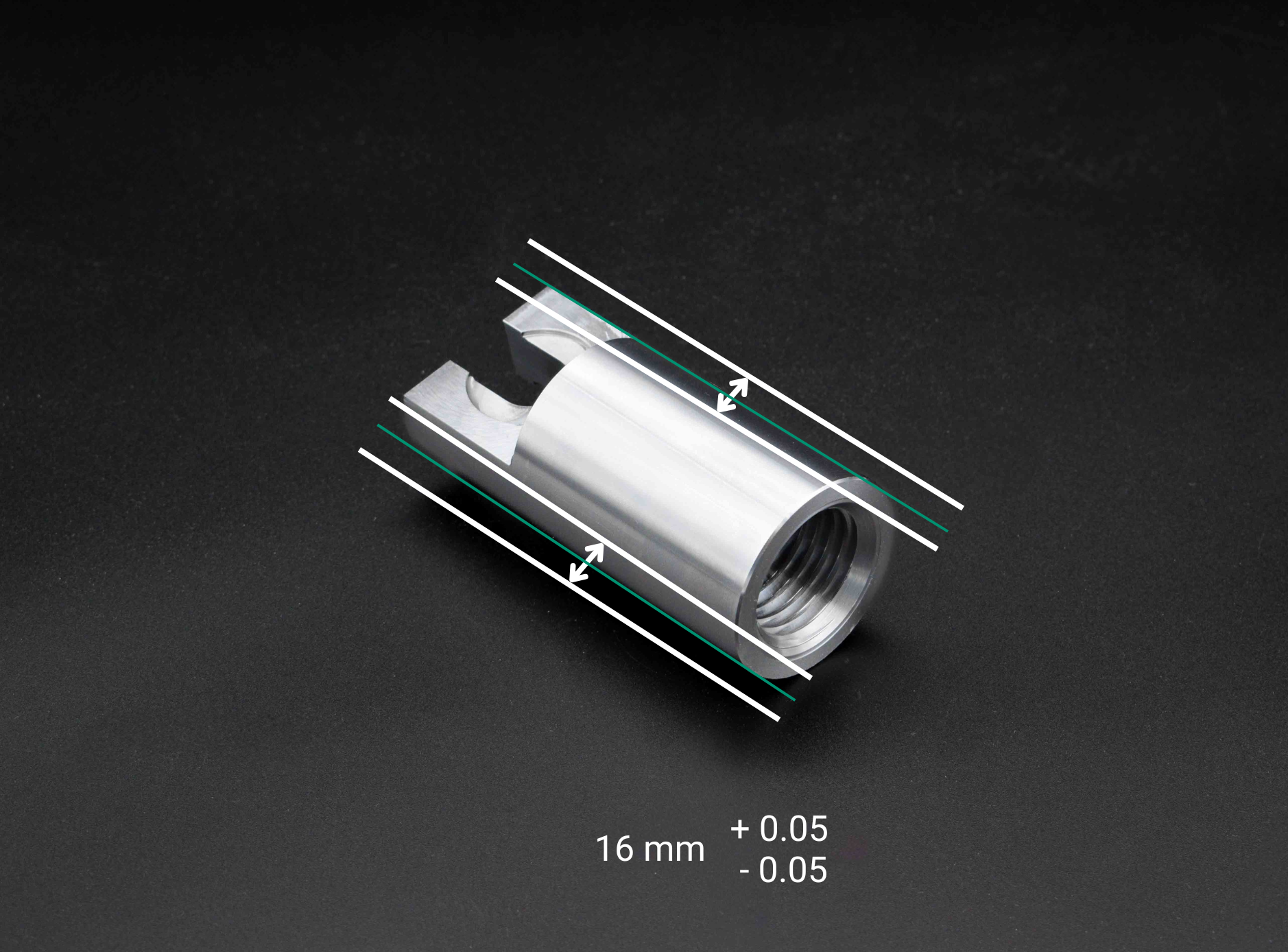
Key Differences Between Unilateral and Bilateral Tolerances
While both tolerance types serve the same goal, dimensional control, they apply it in different ways. Each method has specific strengths depending on how the part functions in an assembly. Understanding when and why to use them helps you avoid costly design and manufacturing issues.
Key Differences | Unilateral Tolerance | Bilateral Tolerance |
---|---|---|
Direction of Variation | Allows variation in only one direction | Allows variation in both directions |
Engineering Drawings | Shown as +0.00/-0.10 or -0.00/+0.10 | Shown as ±0.05 or similar |
Impact on Precision & Quality | Tighter control, ideal for exact fits | More flexible, suited to non-critical features |
Cost & Production Efficiency | Higher cost due to tighter constraints | Lower cost, faster production |
Suitability for Applications | Best for high-precision, load-bearing parts | Ideal for cosmetic or flexible components |
Common Use Cases | Used for fits like shafts and gears | Used for brackets, covers, non-critical features |
Quality Control & Inspection | Simpler, faster inspections in one direction | Requires inspection in both directions |
Direction of Variation
The core difference lies in the direction each tolerance type allows variation from the nominal size. Unilateral tolerances permit deviation in only one direction—either above or below the base size. Bilateral tolerances allow variation in both directions, offering a more balanced tolerance zone.
This difference matters in assemblies where clearance or interference fits are critical. Too much variation in both directions can lead to parts being too loose or too tight. That's why unilateral tolerance is often preferred in high-precision fits.
Bilateral tolerances are ideal when function isn't affected by small dimensional shifts. They're well-suited for non-mating or less sensitive features. This makes them practical for reducing production cost while maintaining acceptable quality.
Engineering Drawings
Unilateral and bilateral tolerances are clearly marked on technical drawings for CNC machining. A unilateral tolerance might be shown as +0.00/-0.10, while a bilateral would appear as ±0.05. These notations ensure machinists and inspectors understand the exact dimensional limits.
In drawings using Geometric Dimensioning and Tolerancing (GD&T), extra symbols like "U" may indicate unequally disposed tolerances. This shows when a bilateral tolerance is intentionally offset more to one side. Accurate notation is essential for maintaining clarity between design and production.
Using a reliable machining drawing service helps ensure these tolerances are applied correctly. It reduces the chance of miscommunication and machining errors. Precise documentation leads to better part quality and fewer delays.
Impact on Precision & Quality
Unilateral tolerances offer tighter control when exact fits are required. This leads to more consistent assemblies and improved long-term performance in critical parts. The one-sided limit makes it easier to stay within necessary parameters.
Bilateral tolerances still support quality but are better suited to features with more leeway. They allow for variation without impacting functionality or appearance. This flexibility can help reduce machining stress and tool wear.
Choosing the correct type of tolerance helps maintain precision where it matters most. It also supports consistent production outcomes and part reliability. Good tolerance planning contributes directly to part quality and product lifespan.
Cost & Production Efficiency
Unilateral tolerances often come with higher machining and inspection costs. Staying within a single-direction limit may require slower speeds, tool changes, or added checks. These costs may be justified for critical features where failure isn't an option.
Bilateral tolerances allow a wider margin of error, which speeds up production. More parts pass inspection on the first try, reducing scrap and improving efficiency. This is especially valuable in high-volume environments with non-critical features.
Making smart tolerance choices directly affects production costs. Overly tight tolerances can lead to unnecessary rework and longer lead times. By matching tolerance type to part function, you can optimise both quality and workflow.
Suitability for Applications
Unilateral tolerance works best for high-precision parts with critical interfaces. This includes shafts, gears, and load-bearing elements where every fraction of a millimetre counts. These parts require strict dimensional control to function correctly.
Bilateral tolerance suits parts with more design freedom or cosmetic requirements. You'll find them in control panels, covers, and faceplates where small dimensional changes won't cause issues. These components benefit from easier machining and faster production.
Material properties also influence which tolerance type to use. Metals and plastics respond differently to temperature and stress, requiring different tolerance strategies. Always consider both part function and material behaviour during design.
Common Use Cases
Use unilateral tolerance for features that must press-fit, rotate, or carry precise loads. It ensures consistent performance in demanding applications like aerospace, defence, or medical equipment. These parts cannot tolerate excess material or movement.
Bilateral tolerance is better for structural or non-mating components. Parts like brackets, spacers, and outer panels don't require exact alignment and are easier to produce with more flexibility. This tolerance type simplifies inspection and lowers overall cost.
Both tolerance types have a place depending on the part's role in the assembly. Knowing where to use each prevents over-engineering and avoids wasted time or resources. It's all about applying the right control where it matters most.
Quality Control & Inspection
Unilateral tolerances simplify inspection by only requiring measurement in one direction. This speeds up checks during production and reduces potential for operator error. It's a practical choice for time-sensitive, high-precision parts.
Bilateral tolerances require inspection in both directions, which takes slightly longer. However, they provide a complete view of dimensional accuracy and part consistency. Modern CMM tools help streamline this process with high-speed, automated checks.
Accurate inspection starts with clearly defined tolerances on the drawing. The more precise the specifications, the more reliable the quality control process will be. Good tolerancing reduces rejects, rework, and long-term quality issues.
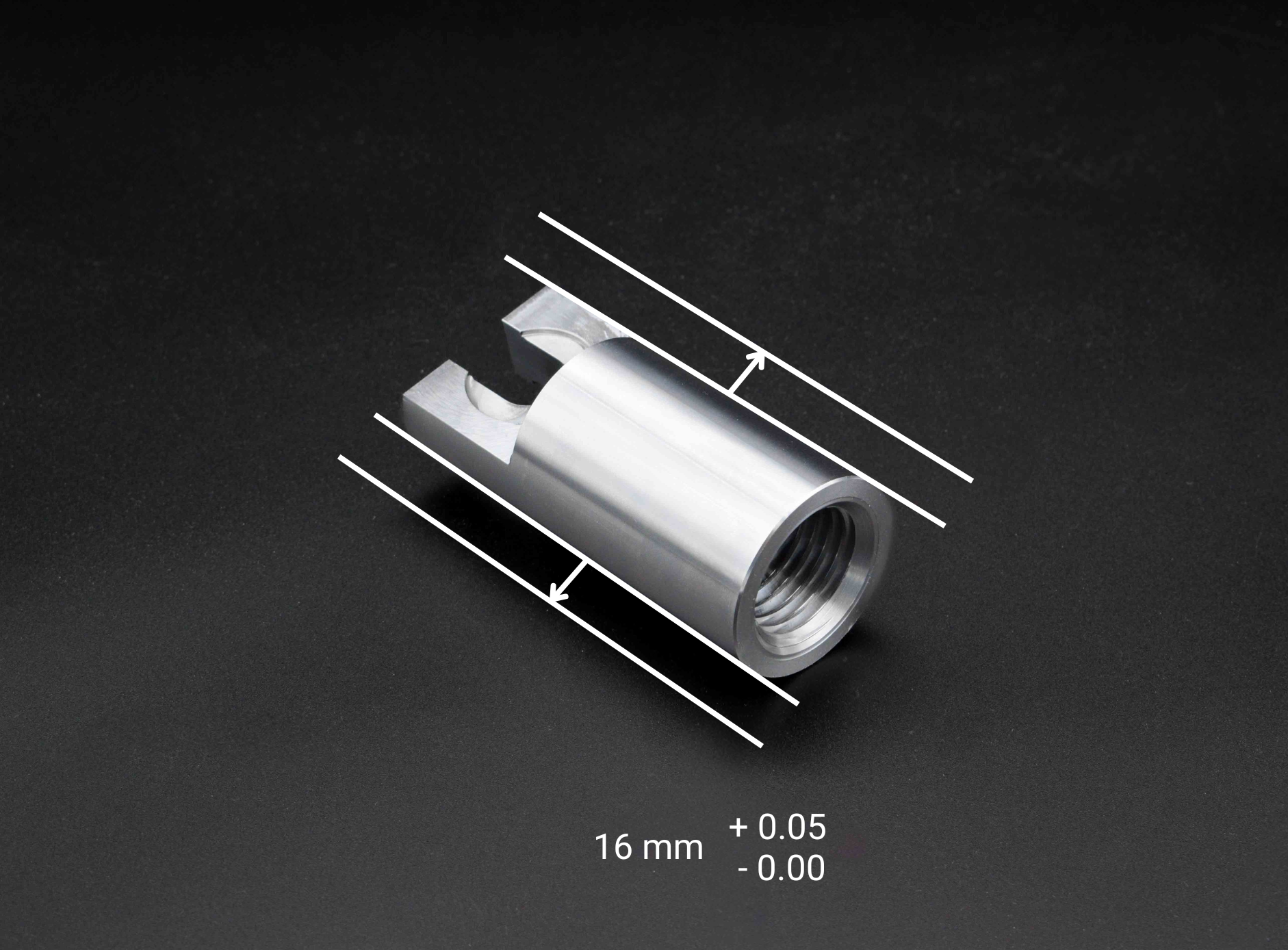
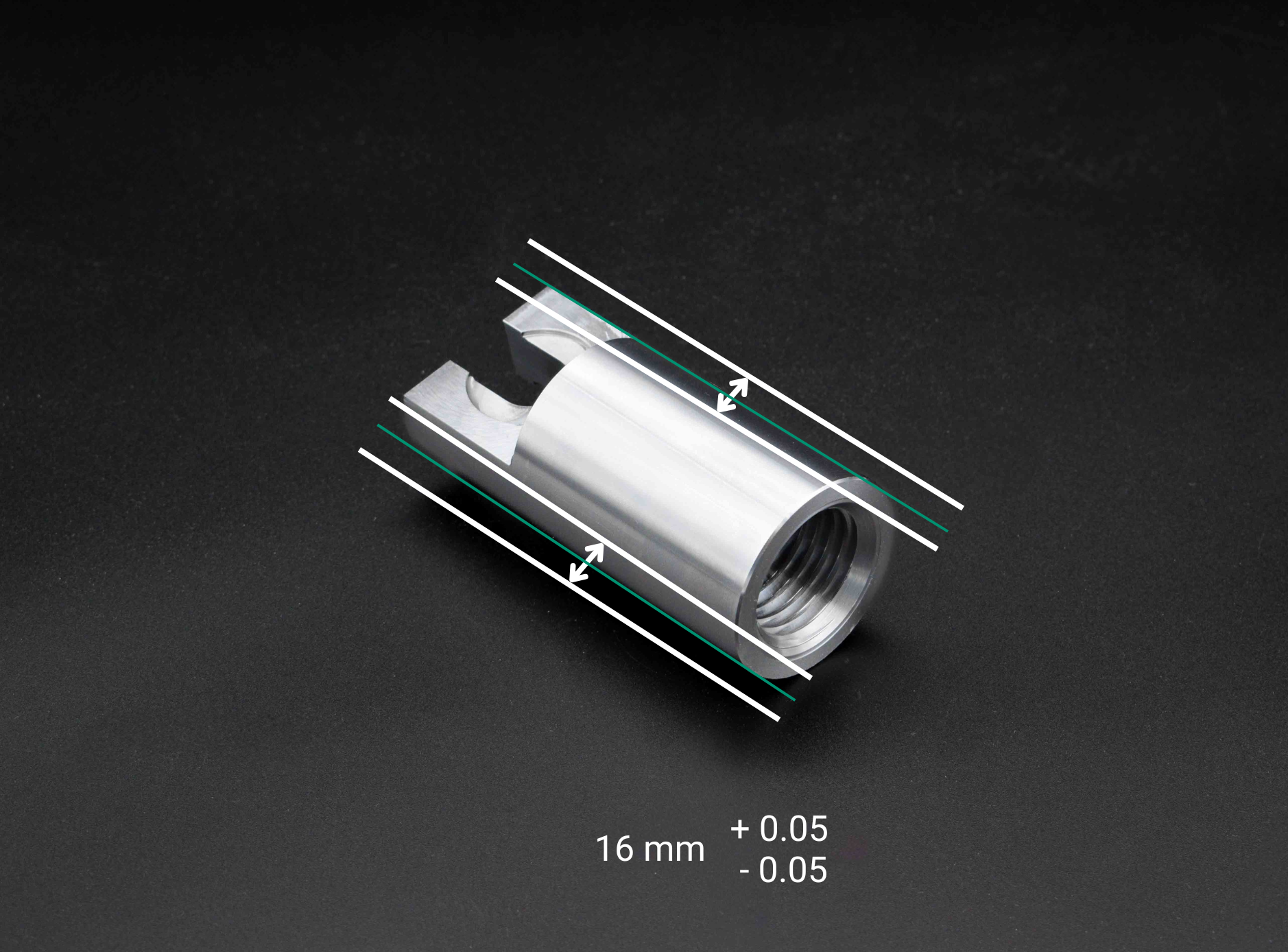
Advantages & Disadvantages
Each tolerance type comes with its own pros and cons depending on your design and manufacturing needs. Understanding these trade-offs helps you choose the most practical and efficient option for your specific application. Below are the key advantages and disadvantages of unilateral and bilateral tolerances.
Unilateral Tolerance
Unilateral tolerance offers high control, making it a strong choice for parts requiring tight fits and precision. It simplifies inspection by limiting variation to one side, which reduces measurement time. However, it can also lead to increased machining time and cost due to tighter constraints.
Advantages:
- Easier to inspect
- Ideal for tight-fitting parts
- Ensures consistent assembly fit
Disadvantages:
- Higher machining costs
- Less flexible
- Slower production in some cases
Bilateral Tolerance
Bilateral tolerance provides more freedom in both design and manufacturing, making it a popular choice for general-purpose components. It allows faster throughput and higher part yield, especially in high-volume production. The trade-off is reduced control, which may impact assemblies that require exact fits.
Advantages:
- More flexible manufacturing
- Faster inspection
- Higher part yield
Disadvantages:
- Less precise fit
- Can cause looseness in assemblies
- More complex dimensional control
Choosing the Right Tolerance
Choosing between unilateral tolerance vs bilateral tolerance depends on your design priorities and how the part will function in its final application. If you need tight fits, minimal variation, or critical alignment, unilateral tolerance is usually the right choice. When speed, cost, and manufacturing flexibility are more important, bilateral tolerance often makes more sense.
Consider the role of the part in the assembly and how much variation it can tolerate without affecting performance. Material type, expected thermal expansion, and surface finish also influence which approach to use. Balancing function, manufacturability, and cost is the key to effective tolerance selection.
Your CNC supplier can offer insights based on their capabilities, tools, and inspection methods. A collaborative approach is especially helpful when working with tight tolerances or complex assemblies. Partnering with a trusted CNC machining service helps reduce risk, improve part quality, and ensure a smoother production process.
Key Takeaways on Tolerances in Engineering
Tolerances define the acceptable range of variation in a part's dimensions, which directly impacts function, fit, and manufacturability. They affect how easily parts assemble, how thoroughly they must be inspected, and how costly they are to produce. Getting tolerances right is essential to ensuring consistent, reliable performance in any application.
Bilateral vs unilateral tolerance isn't about which one is better overall, it's about choosing the right tool for the job. Each method suits different needs depending on the part's role, material properties, and required precision. Making the correct choice leads to fewer production issues and better long-term results.
Use tighter tolerances only where needed, such as for high-precision fits or load-bearing components. Apply looser tolerances in non-critical areas to save on cost, time, and material waste. This balance also improves communication with machinists and streamlines collaboration with CNC suppliers.